インサート成形とは?特徴や種類、メリット・デメリットを解説!
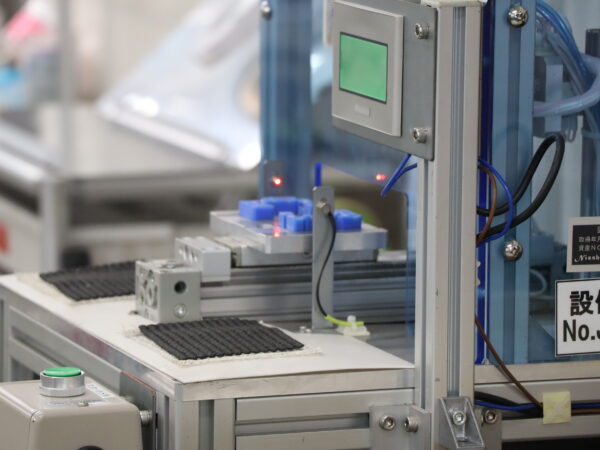
製造業において、異なる材料を組み合わせて一体成形する技術は、製品の特性や機能性を飛躍的に向上させるための重要な手段です。その中でも「インサート成形」は、金属と樹脂、もしくは異なる種類の樹脂同士を一体化させることで、強度の向上や軽量化、耐久性の強化を実現する優れた技術です。また、インサート成形は、電子機器や自動車、医療機器など、製品に高い性能や複雑な機能が求められるさまざまな分野で広く採用されており、部品の信頼性を高め、製造プロセスの効率化にも大きく貢献しています。
特に、金属の強度と樹脂の軽量性といった異なる材料の特性を組み合わせることで、従来の単一素材では得られない製品特性を実現できる点がインサート成形の最大の特徴です。この技術は、製品の耐熱性や耐衝撃性の向上、コスト削減など、多様なメリットをもたらすため、日々進化を遂げています。
今回の記事では、インサート成形の基本的な知識や特徴、さらには製造時におけるメリットやデメリットについて解説します。
インサート成形とは?
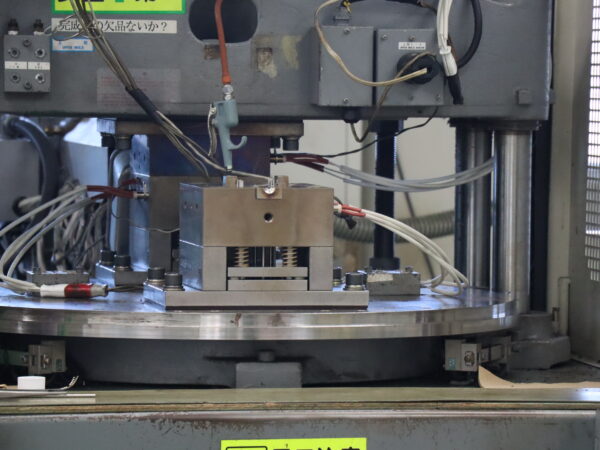
インサート成形とは、金属やプラスチックなどの異なる材料を一体化させて製品を成形する技術です。この成形方法は、金型の中にインサート(部品)を配置し、そこに樹脂などを注入することで、一体化した製品を作り出します。インサート成形の主な利点は、複数の工程をまとめて一つの成形品にすることができる点です。これにより、製作コストの削減や生産効率の向上が期待できます。
この技術は、電子機器や自動車、医療機器など、耐久性や強度が求められる分野で特に活躍しています。金属と樹脂を組み合わせることで、軽量でありながらも高強度な部品を作成することが可能です。さらに、形状や機能を自在に調整できるため、さまざまな用途に適応することができます。
インサート成形の工程
インサート成形は、金型にインサート部品を配置し、樹脂を射出して一体化した製品を作り出す高度な成形技術です。この工程では、部品の正確な配置と材料の選定が製品の品質を大きく左右します。以下は、インサート成形の主要な工程です。
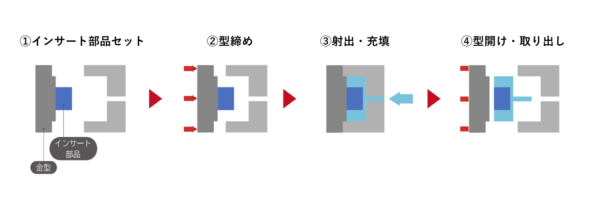
インサート部品の配置
インサート成形における最初の重要な工程は、インサート部品を正確に金型内に配置することです。この工程は手作業、またはロボットによる自動作業で行われます。少量生産では手作業が一般的ですが、大量生産ではパーツフィーダーなどを使用して部品を機械的に自動配置します。ここでの正確な配置が、成形後の製品の形状や性能に大きく影響を与えるため、フィルムやガイドを用いるなどして、インサート部品が動かないように工夫されています。インサート部品の固定がしっかりと行われることで、成形時のズレや製品の不良を防ぐことができます。
型締め
インサート部品が配置された後、型締めの工程が行われます。この工程は通常の射出成形と同じです。金型がしっかりと閉じられることで、後に続く工程で樹脂が正確に流れ、均一な製品を成形できるように準備されます。正確な型締めが、最終的な製品の品質に大きく影響を与えます。
射出・充填
型締めが完了すると、溶融樹脂が金型内に射出されます。この段階で、樹脂はインサート部品を包み込むように流れ込みます。樹脂は、インサート部品を確実に固定しつつ、製品全体を一体化させます。樹脂の温度管理や流動性は、製品の仕上がりに大きく影響するため、この工程では精密な制御が必要です。
型開け・取り出し
樹脂が固化した後、金型を開き、完成した製品を取り出します。この時、製品とインサート部品が一体化しているため、後工程での組付け作業が不要となり、生産の効率化が図れます。成形後、製品は冷却され、仕上げの工程に進みます。
インサート成形は、それぞれの方法が持つ特長を活かし、多様な材料を組み合わせることで、機能的で高付加価値な製品を実現します。
インサート成形の種類とその特徴
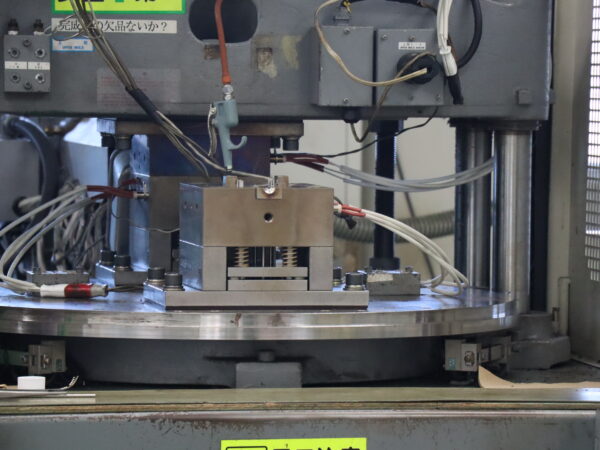
インサート成形は、製造工程において異なる材料を一体化させる技術です。使用する部品や成形方法に応じていくつかの種類に分類され、それぞれの特性を活かすことで、製品の性能向上に寄与しています。
以下では、主なインサート成形の種類とその特徴についてご紹介します。
- 金属インサート成形
金属インサート成形は、金属部品と樹脂を組み合わせることで、製品に高い強度と耐久性を持たせる技術です。通常、金型に金属部品をセットし、その上から溶融した樹脂を流し込み、一体化させます。これにより、ねじや軸といった機械的な強度を必要とする部品に適した構造を形成します。例えば、自動車のエンジン部品や産業機械のハウジングなど、厳しい使用環境での耐久性が求められる部品に多く用いられています。
- 二色インサート成形
二色インサート成形では、異なる種類の樹脂を組み合わせて製品を成形します。たとえば、硬度の異なる材料を使用することで、柔軟性や耐衝撃性を向上させることが可能です。自動車の内装部品や電子機器のコネクタなど、機能性とデザイン性を兼ね備えた製品に適用され、外観と性能の両方を向上させます。
- 複合材料インサート成形
複合材料インサート成形は、炭素繊維(CFRP)や繊維強化プラスチック(FRP)を使用し、軽量かつ高強度の部品を製造する技術です。この方法は、自動車のシャーシや航空機の部品、スポーツ用品など、軽量化が求められる分野で特に効果的です。これにより、製品性能の向上と耐久性の強化が実現します。
インサート成形は、多様な材料と技術を組み合わせることで、製品の特性を最大限に引き出す成形方法です。各種成形技術が持つ特長を活かし、金属や樹脂などの異なる材料を一体化することで、機械的強度や耐久性、機能性を備えた高付加価値な製品を実現します。これにより、自動車部品や電子機器、医療機器といった多様な分野で、より機能的で高性能な製品が提供されています。
このように、インサート成形技術はその応用範囲が広く、多様な用途に適用可能な技術です。
インサート成形のメリットとデメリット
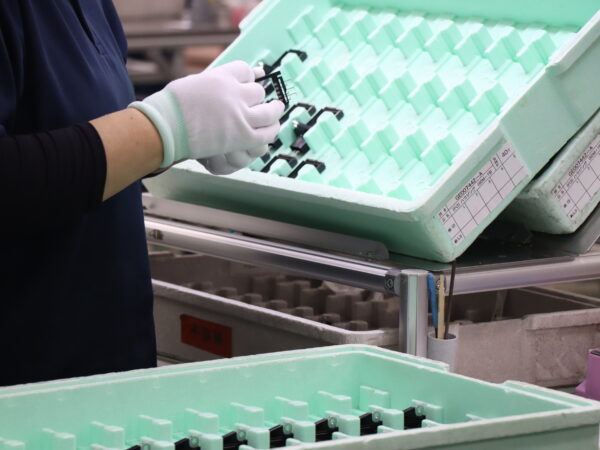
インサート成形にはさまざまなメリットとデメリットがあり、それらを理解することで、製品の設計や製造において最適な選択ができます。
以下に、主なメリットとデメリットをそれぞれ紹介します。
- メリット
- 強度・耐久性の向上
インサート成形では、金属と樹脂といった異種材料を組み合わせて使用することで、個々の材料の特性を補完し合い、製品全体の強度と耐久性を高めることが可能です。特に、耐熱性や耐衝撃性が求められる場合、インサート成形の優れたパフォーマンスが発揮されます。例えば、自動車部品や電化製品など、厳しい使用環境下でも製品の性能を維持し、信頼性を向上させることができます。
- 生産工程の効率化と生産コスト削減
インサート成形は、複数の部品を一体化することができるため、従来の組み立て工程を簡略化し、生産効率を高めます。これにより、コスト削減を実現し、部品の精度も向上することができます。たとえば、電子機器やプラスチック製品の内部構造では、部品をまとめて成形することで、工程の簡素化と高い精度を両立させることが可能です。
- 高い設計自由度と機能性の向上
インサート成形は、複雑な形状や多機能を実現できる技術であり、他の成形技術では対応できない部分も補うことが可能です。特に、電子部品や自動車の内装部品などでは、精密な設計と耐久性を両立させるために多用されており、機能とデザイン性を融合させた製品の開発が可能になります。
- デメリット
- 成形不良のリスク
異なる材料を組み合わせる場合、収縮率や膨張率が異なるため、成形時にひずみや歪みが発生するリスクがあります。これにより、製品の精度や品質に悪影響を及ぼす可能性があります。正確な成形条件の設定と材料選定が成形成功の鍵となります。
- 初期コストと技術力の要求
インサート成形には、複雑な金型や専用の設備が必要なため、初期投資が大きくなります。また、成形条件の管理や材料の組み合わせに熟練した技術力が求められ、専門的な知識とスキルを持つ作業者が必要不可欠です。
- 材料間の接合強度のムラ
異なる材料同士の接合部分において、接合強度にムラが生じることがあります。特に、材料の熱膨張率の差が原因で接合部が弱くなる可能性があり、これが強度不足や耐久性の低下につながることもあります。
インサート成形は、これらのメリットとデメリットを考慮しながら、適切な材料と成形条件を選定することで、幅広い分野で機能的で高品質な製品を実現することが可能です。
インサート成形に適した材料と用途
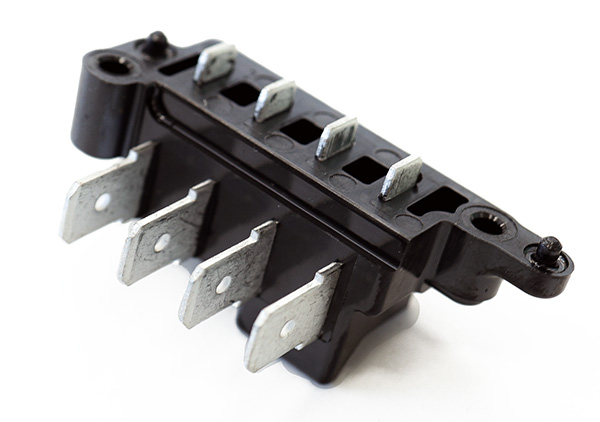
インサート成形に適した材料は、成形する製品の特性や用途に応じて選択されます。以下は代表的な材料とその用途です。
- プラスチック材料
プラスチック材料は、インサート成形において非常に多く使用される基材であり、さまざまな産業で重宝されています。例えば、ポリプロピレン(PP)は軽量かつ耐衝撃性が優れており、自動車の内装部品や家電製品に使用されます。ポリカーボネート(PC)は、透明性が高く、耐衝撃性と耐候性に優れるため、光学部品や電子機器のケースとしてよく利用されます。これらの材料は、製品の軽量化や耐久性の向上を目的に、主に自動車、医療機器、家電製品などで活用されています。加えて、複雑な形状や精度の高い加工が可能であり、特に精密機器の製造に適しています。
- 金属材料
インサート成形では、金属材料も重要な役割を果たします。アルミニウムやステンレス鋼などの軽量で耐久性のある金属は、自動車部品や航空機部品に頻繁に使用されます。たとえば、自動車のエンジン部品では、金属の強度と樹脂の軽量性を組み合わせることで、耐久性の高い部品を製造できます。また、ステンレス鋼は、耐腐食性に優れ、電子機器のコネクタやボルトのような高い機械的強度が要求される部分に最適です。金属インサートの使用により、製品の強度が向上し、耐久性が求められる産業で広く採用されています。
- 複合材料
複合材料は、金属や樹脂に繊維強化プラスチック(FRP)や炭素繊維(CFRP)を加えることで、軽量でありながら高強度を実現する素材です。この材料は、特に軽量化が求められる自動車のシャーシや航空機の構造部品に用いられ、車体の重量を削減しつつ、耐久性を保つ役割を果たしています。また、スポーツ用品の製造においても、複合材料は欠かせない存在であり、例えばラケットやゴルフクラブでは、強度と柔軟性を兼ね備えた製品を実現します。これにより、パフォーマンスの向上が期待でき、製品の付加価値が高まります。
インサート成形とは?まとめ
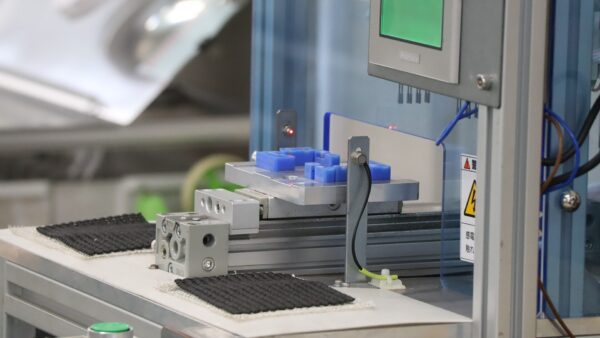
インサート成形は、異なる材料を組み合わせることで、単一材料では得られない特性や機能を付加できる成形技術です。金属や樹脂といった材料を一体化し、軽量化や強度の向上、耐久性の強化を実現し、さらには電気伝導性を持たせることが可能です。この技術は、自動車、電子機器、医療機器など多岐にわたる産業で広く活用され、特に製品の設計の自由度を広げることで、品質の向上に大きく貢献しています。
射出成形におけるインサート成形の工程では、まずインサート部品を金型に配置し、樹脂を射出することで、一体化した製品を成形します。これにより、プラスチックと金属の異なる材料を組み合わせることで、強度と軽量性を兼ね備えた製品が製作されます。例えば、自動車の部品では、燃費向上や耐久性の向上を実現するために活用されています。
ただし、この成形方法にはデメリットもあり、材料選定や高精度な加工技術が求められる点や、製造コストの増加が挙げられます。インサート成形には、精密な金型設計と正確な材料管理が不可欠で、製品の仕上がりや耐久性に影響を与えます。
根本電工株式会社では、インサート成形の高度な技術を活かし、プラスチック製品と金属部品を融合させた高品質な部品の製作を行っています。特に、異種材料の一体化を通じて、製品の安全性と耐久性を向上させることで、さまざまな産業のニーズに対応しています。インサート成形に関するご相談やお悩みがございましたら、ぜひお気軽にお問い合わせください。

お問い合わせ
Contact
技術的なご相談からお見積りの依頼まで
お気軽にご相談ください。
メールでのお問い合わせはコチラ
お電話でのお問い合わせはコチラ
(0293)24-0567
営業時間:8:00~17:00
お問い合わせ
Contact
技術的なご相談から
お見積りの依頼まで
お気軽にご相談ください。
メールでのお問い合わせはコチラ
お電話でのお問い合わせはコチラ
(0293)24-0567
営業時間:8:00~17:00