よくわかる!プラスチック成形の基本「射出成形」とは?製造工程、メリット・デメリットを解説!
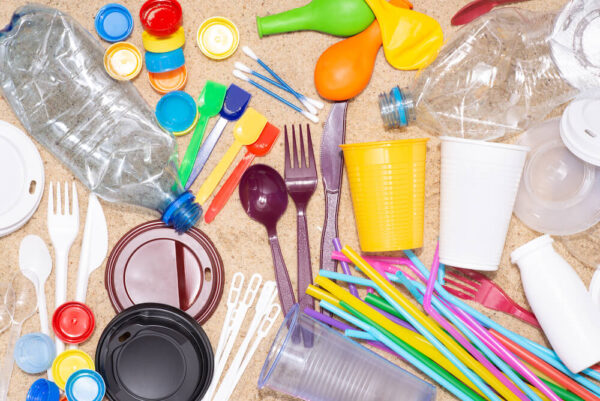
私たちの暮らしに欠かせない存在のプラスチック。自動車部品やテレビ・洗濯機といった電化製品、スマホ、日用品にいたるまで私たちの身の回りにはたくさんのプラスチック製品があります。
そのプラスチック製品を成形する方法は、圧縮成形、ブロー成形、押出成形、真空成形などさまざまな工法がありますが、その中で最もメジャーなプラスチック成形工法が「射出成形」です。
今回の記事では、射出成形の概要や仕組み、メリット・デメリットについて紹介します。
射出成形(Injection Molding)とは?成形機の構造について
射出成形とは、プラスチック樹脂などの材料を加熱溶融させ、金型に送り込み、冷却することで形を作る成形法です。注射器で液体を送り込む様子に似ていることから、「射出成形」と呼ばれています。インサート成形やインジェクション成形ともいいます。
金型を使用するため、同じ形状の製品を短時間に大量生産することが可能で量産性と安価さに優れています。また、金型の転写性が非常に高いため、複雑で多様な形状の製品を製造することもできます。そのため、日用品をはじめ生活に身近なプラスチック製品の多くは射出成型によって作られています。
射出成形では、射出成形機と呼ばれる専用の機械を使用します。
射出成形機は主に以下のような構造で構成されています。
- 射出装置
材料を加熱し溶融し、金型へ高圧で射出する装置です。内部には「ホッパー」「スクリュー・シリンダー」「ノズル」という3つの主要部品があります。
ホッパー:材料投入口
スクリュー・シリンダー:材料を加熱・混錬し、送り出す装置
ノズル:溶融した材料を金型に射出する部分
- 型締め装置
金型を固定し、締めつけや開閉を行う装置です。内部は可動側と固定側のダイプレート、型締シリンダーから構成されています。材料の射出後、冷却する役割もあります。
- コントローラー
コントローラーは射出成形機の制御をする部分です。成形に必要な条件である射出速度や温度、射出量などを管理する装置です。コントローラーは内蔵されているものもあれば、外付けのものもあります。
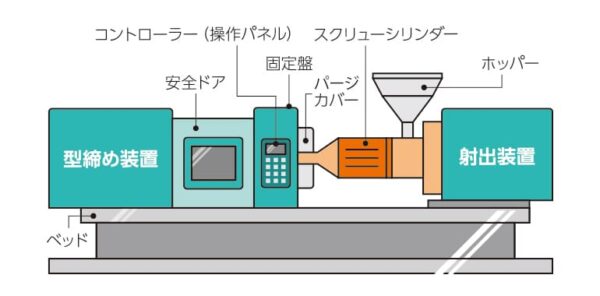
引用:株式会社関東製作所
射出成形機には大きく分けて横型と竪型の2種類がありますが、成形品を金型から取り出す際に取り出しやすいことから、一般的には横型射出成形機がよく利用されます。また、射出や型締めに必要な動力源による分類では、サーボモータで作動する電動式、油圧モータを用いた油圧式、サーボモータと油圧モータを組み合わせたハイブリッド式などに分かれます。
近年では射出成形機のCNC化が進み、コントローラーの制御により精度の高い製品の高速射出が可能な機種も普及してきています。
射出成形の製造工程
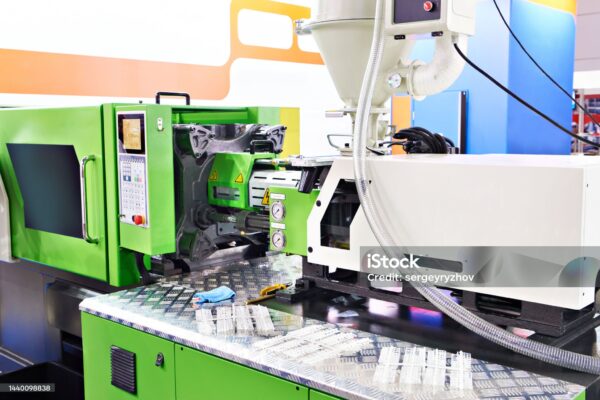
続いて、射出成形の流れを以下に紹介します。
- 材料の投入
ホッパーに乾燥させた粒状(ペレット状)のプラスチック材料を投入します。
- 材料の溶融・計量
粒状のプラスチック材料がシリンダー内へ送られ、シリンダー内部のヒーターが搭載されたスクリューが回転することにより、溶融・混錬されながら先端部分(計量ゾーン)に運ばれます。
- 型閉じ・型締め
型締め装置の可動側に雄の金型、固定側に雌の金型を取り付け、閉じて締め付けます。プラスチック材料を射出する際には高い圧力が金型にかかるため、金型が開かないよう強い締め付けが必要になります。
- 材料の射出
シリンダー先端のノズルを金型に押し付け、圧力をかけながら溶融したプラスチック材料を金型内に射出します。
- 保圧・冷却・固化
圧力をかけながら(保圧)冷却し、プラスチック材料が固まるのを待ちます。その間に、次の成形用のプラスチック材料(ペレット)を溶かして溜めておきます。
- 型開き
プラスチック製品が固まったら金型を開きます。
- 製品の取り出し
突き出し装置(エジェクターピン)で、完成した成形品を取り出します。
このようなサイクルを何度も繰り返し、製品を量産していきます。
射出成形のメリット・デメリット
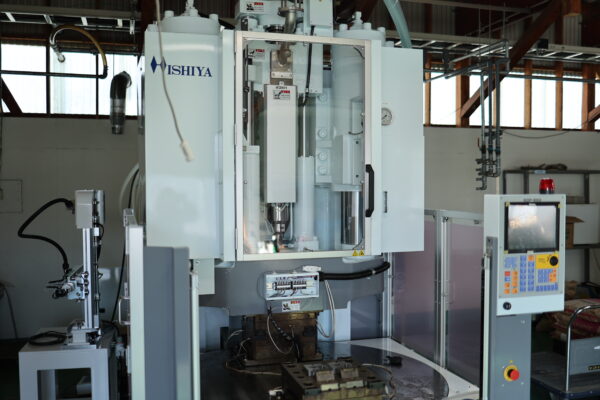
次に、射出成形のメリット・デメリットをご紹介します。
- メリット
- 大量生産が可能
一度金型を製作してしまえば、同品質・同形状の成形品を大量に作ることができます。また、1回の成形にかかる時間が秒単位であり、一つの金型で複数の成形を行うことも可能なので、短期間で非常に多くの製品を作ることができます。金型製作後は、材料代しかかからないので、コストも抑えることができます。そのため射出成形は大量生産に適しています。
一般的には定期的に金型メンテナンスを行った場合、一つの金型で約100万個の製品を成形することが可能です。
- 高品質な製品を生産できる
成形機上で、閉じられた金型の中に高圧力で溶けた樹脂を注入するため金型の転写性が非常に高く、複雑な形状や細かいディテールの製品も高精度で製造できます。
また、射出成形機の加熱・冷却、材料供給、金型の開閉などの制御することにより安定した品質の製品を製造することができます。
- さまざまなサイズの製品に対応できる
直径1mm未満の小さいものから、車のバンパーなど大きなものまで幅広いサイズに対応できます。
対応可能な大きさは、射出成型機のサイズによって異なります。
- さまざまな樹脂材料に対応できる
射出成形は溶融した樹脂を金型に流し込んで成形するため、溶融してしまえばどのプラスチック材料でも概ね対応できます。そのため幅広い種類のプラスチック材料が使用可能です。
- 後加工が少ない
射出成形では表面の質感や微細な部分まで精密に成形できるため、多くの場合は成形後にゲートなどの切り離しとバリ取りを行う程度で成形品がそのまま完成品となります。そのため、仕上げ加工などの後工程が不要なことが多く、手間がかかりません。
- デメリット
- 金型製作に時間がかかる
射出成形では、製品に合わせて金型を作らなければいけません。試作や設計変更などの改良が必要な場合も多く、製作時間は数カ月程度かかることもあります。そのため、短納期の製品の場合は、他の加工法で製作した方が良いでしょう。
- 金型製作にコストがかかる
前述の通り、製品ごとに金型を設計・製作しなければならないため、費用も高額になります。多品種少量生産にはコストがかかるため、向いていません。
- 製品形状やサイズに一部制約はある
幅広い形状の製品に対応できる射出成形ですが、樹脂が硬化した後に金型から取り外せる形状にしなければなりません。金型から製品を取り出すための「抜き勾配」などを考慮して設計することが必要になります。また、対応可能サイズは幅広いものの、非常に大きい形状や非常に小さい形状、肉厚が厚すぎたり薄すぎたりする形状では、作ることができないことや不良率が高くなることがあります。
射出成形とは? まとめ
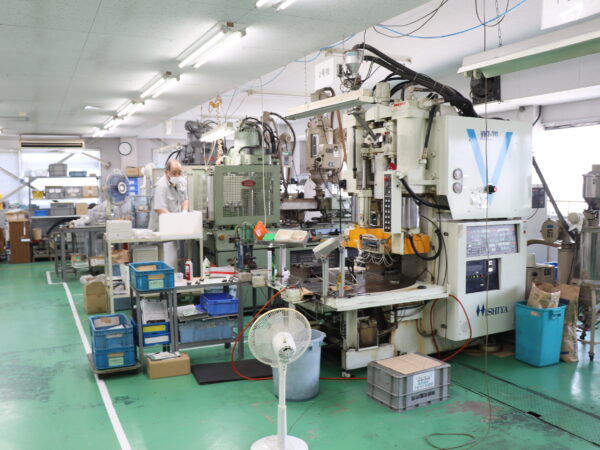
射出成形は、自動車部品から家電、医療機器まで、私たちの生活に欠かせないプラスチック製品を製造する最もメジャーで重要な成形工法です。超大量生産ができ、さまざまな樹脂材料に対応可能で多様で高精度の製品が製造できることから、非常に優れた製造技術と言えるでしょう。
そんなメリットがたくさんある射出成形ですが、高品質な製品を効率よく作るには、整った設備と材料選びから金型設計、成形条件の調整など経験から培った技術的な知見が重要になります。
根本電工株式会社では、長年射出成形によるプラスチック製品の製造に携わってきました。その豊富な実績により、高性能・高品質なプラスチック製品の提供が可能です。プラスチック製品の製造に関するご依頼をご検討中の方は、お気軽に当社までご相談・お問い合わせください。

お問い合わせ
Contact
技術的なご相談からお見積りの依頼まで
お気軽にご相談ください。
メールでのお問い合わせはコチラ
お電話でのお問い合わせはコチラ
(0293)24-0567
営業時間:8:00~17:00
お問い合わせ
Contact
技術的なご相談から
お見積りの依頼まで
お気軽にご相談ください。
メールでのお問い合わせはコチラ
お電話でのお問い合わせはコチラ
(0293)24-0567
営業時間:8:00~17:00