インサート成形に使用される金型とは?構造や高品質な製造ためのポイントについて分かりやすく解説!
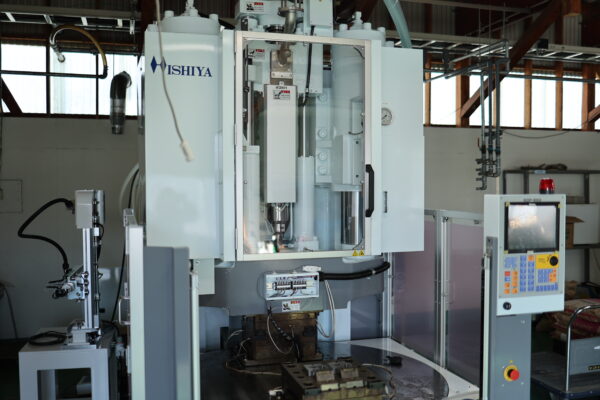
インサート成形は、金属部品やプラスチックなどの異なる材料を一体化させて製品を成形する射出成型技術です。特に、自動車や電気電子部品、精密機器など、耐久性や機能性が求められる分野で広く活用されています。近年、電気自動車や半導体市場の成長をはじめ、技術革新が著しい状況からも小型・高性能化を実現するためにもインサート成形部品においてもより高い品質が求められています。そんなインサート成形においては「金型」が非常に重要な役割を果たし、その設計や管理が製品品質を大きく左右します。
本記事では、インサート成形のメカニズムから金型構造、さらには生じやすい不良・欠陥について詳しく解説します。不良・欠陥の対策に関しては本記事では簡易的に紹介したいと思います。簡単にインサート成形の金型に関する理解を深め、自社製品の品質向上にお役立てください。
インサート成形のメカニズム
インサート成形とは?
インサート成形とは、金属やプラスチックなどの異なる材料を一体化させて製品を成形する技術です。この成形方法は、金型の中にインサート(部品)を配置し、そこに樹脂などを注入することで、一体化した製品を作り出します。インサート成形の主な利点は、複数の工程をまとめて一つの成形品にすることができる点です。これにより、製作コストの削減や生産効率の向上が期待できます。また、金属が電流を流すのに対して、プラスチックなどの樹脂は電流をほとんど伝えない性質があるため、樹脂で電流を遮断する効果を得ることができ、特に、電気系におけるコネクタやリレー、遮断機などの電気部品にインサート成形部品がよく用いられています。
この技術は、電子機器や自動車、医療機器など、耐久性や強度が求められる分野で特に活躍しています。金属と樹脂を組み合わせることで、軽量でありながらも高強度な部品を作成することが可能です。さらに、形状や機能を自在に調整できるため、さまざまな用途に適応することができます。
インサート成形の特長
- 強度・耐久性の向上
インサート成形では、金属と樹脂といった異種材料を組み合わせて使用することで、個々の材料の特性を補完し合い、製品全体の強度と耐久性を高めることができます。特に、耐熱性や耐衝撃性が求められる場合、インサート成形の優れたパフォーマンスが発揮されます。例えば、自動車部品や電化製品など、厳しい使用環境下でも製品の性能を維持し、信頼性を向上させることができます。
- 生産工程の効率化と生産コスト削減
インサート成形は、複数の部品を一体化することができるため、従来の組み立て工程を簡略化し、生産効率を高めます。これにより、コスト削減を実現し、部品の精度も向上することができます。たとえば、電子機器やプラスチック製品の内部構造では、部品をまとめて成形することで、工程の簡素化と高い精度を両立させることが可能です。
- 高い設計自由度と機能性の向上
インサート成形は、複雑な形状や多機能を実現できる技術であり、他の成形技術では対応できない部分も補うことが可能です。特に、電子部品や自動車の内装部品などでは、精密な設計と耐久性を両立させるために多用されており、機能とデザイン性を融合させた製品の開発が可能になります。
インサート成形の基本工程
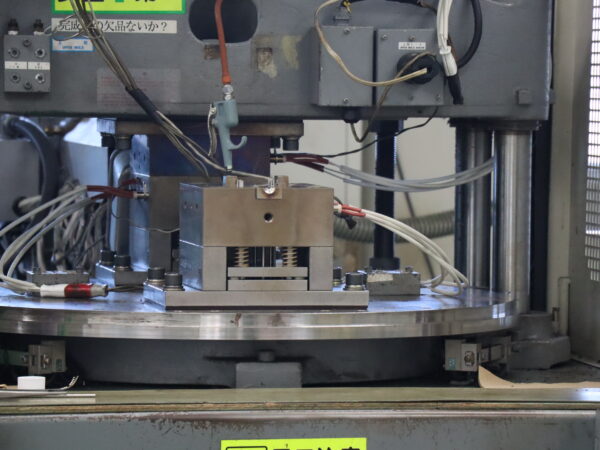
弊社にて実際にインサート成形機のセットアップを行っている様子
- インサート部品の配置
インサート成形における最初の重要な工程は、インサート部品を正確に金型内に配置することです。この工程は手作業、またはロボットによる自動作業で行われます。少量生産では手作業が一般的ですが、大量生産ではパーツフィーダーなどを使用して部品を機械的に自動配置します。ここでのインサート部品の正確な配置が、成形後の製品の形状や性能に大きく影響を与えるため、フィルムやガイドを用いるなどして、インサート部品が動かないように各社のノウハウも生かして工夫して行われることが一般的です。インサート部品の固定がしっかりと行われることで、成形時のズレや製品の不良を防ぐことができます。
弊社では、代表を務める根本が元々自動化ラインの設計を行っていた技術者であったため、射出成形の製造ラインにおけるパーツフィーダーの自社開発等、省力化と部品配置の精度を高めるハードウェアを含めたシステムの開発を行えるため、高い品質の製品の提供を可能にしております。 - 型締め
インサート部品が配置された後、型締めの工程が行われます。この工程は通常の射出成形と同じです。金型がしっかりと閉じられることで、後に続く工程で樹脂が正確に流れ、均一な製品を成形できるように準備されます。もちろん、この時、金型の寸法精度などが基準となるレベルで製造されていないと、適切な型締めが行えない場合もあります。正確な型締めが、最終的な製品の品質に大きく影響を与えるため、金型の設計/製造も含め、この工程は重要な工程であると言えます。 - 射出・充填
型締めが完了すると、溶融樹脂が金型内に射出されます。この段階で、樹脂はインサート部品を包み込むように流れ込みます。樹脂は、インサート部品を確実に固定しつつ、製品全体を一体化させます。樹脂の温度管理や流動性は、製品の仕上がりに大きく影響するため、この工程では精密な制御が必要であり、製品が精密品である場合は、温調機やホットランナーシステム、多段階の射出制御が可能な高機能な設備を利用することをおすすめします。弊社では、射出速度5段階、保圧3段階、軽量速度と背圧(樹脂を溶かして送り出すスクリュー(ねじ状の部品)が後退する際にかける圧力)も3段階の制御が可能であることなど、複雑な加工条件の設定を実現できる菱屋精工(株)製のVNT-100R/Sをはじめとした射出成型機を多数そろえており、高品質な製品の加工を行っております。 - 型開け・取り出し
樹脂が完全に固化した後、金型を開いて完成した製品を取り出します。取り出しには、エジェクターピン(製品を押し出すピン)やロボットアームが用いられ、成形品に傷がつかないよう慎重に行うことが重要です。この時、インサート部品が樹脂と一体化しているため、後工程での組付け作業が不要となり、生産の効率化が図れます。取り出し後、製品は冷却されますが、冷却が不十分だと製品の変形や寸法精度のばらつきが発生するため、金型内での冷却時間を適切に管理する必要があります。また、取り出し時にインサート部品がズレていないか、成形品にバリ(余分なはみ出し)や傷がないかを確認することも重要です。その後、製品は仕上げの工程へと進み、不要な部分のトリミングや外観検査が行われ、最終製品として仕上げられます。
その他インサート成形に関しては別の記事でも解説しております。より基礎知識について詳細を知りたい場合には、以下記事をご確認ください。
インサート成形の金型構造
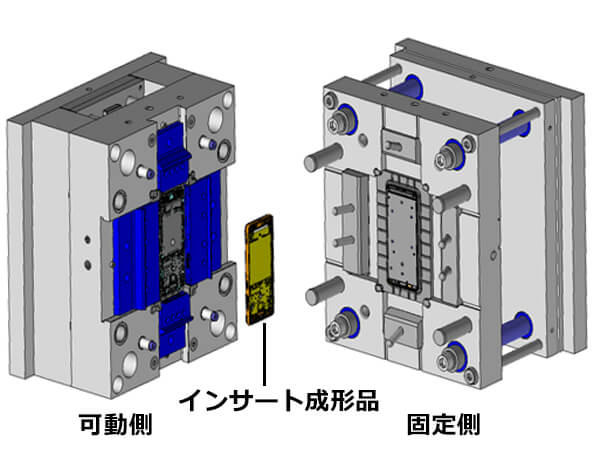
引用:三光ライト工業株式会社様 - 「インサート成形とは?」
高品質なインサート成形加工を実現するためには、金型の構造が重要な要素となります。特にインサート部品の固定や樹脂の流動設計が製品の品質に大きく左右します。以下では、金型の基本構成要素や、設計における重要なポイント、欠陥・不良などのリスクについて解説します。
金型の基本構成
射出成型加工は、設置場所の制限が少なく量産効率が高い横型の射出成型機が主流です。一方でインサート成形の場合、インサート(金属)を固定しなければならないため竪型の射出成型機がよく用いられています。横型においてもインサート成形が可能な場合がありますが、竪型の場合インサートの位置決めに加えて、複数個の金型をテーブルを回転させることで順番に使用できるロータリーテーブルを用いた生産効率の向上も可能であるため、インサート成形を行う上では竪型成形機の方が有利とされています。
- 固定側金型(キャビティ)
金属基材は、高い機械的強度や耐久性が求められる製品に使用されます。例えば、自動車部品、工具、電子機器の接点部分などで多く用いられます。ステンレスやアルミニウムが一般的で、電気伝導性や耐熱性も確保できます。
- 可動側金型(コア)
プラスチック基材は、軽量化と設計自由度の高さが求められる製品に適しています。ABSやポリカーボネート、ポリアミドなどの熱可塑性樹脂がよく使用されます。電子機器のケースや家庭用品など、幅広い用途で活用されています。
- インサート固定機構
プラスチック基材は、軽量化と設計自由度の高さが求められる製品に適しています。ABSやポリカーボネート、ポリアミドなどの熱可塑性樹脂がよく使用されます。電子機器のケースや家庭用品など、幅広い用途で活用されています。
- 冷却機構
樹脂を効率よく冷却し、固化を促す冷却水路が配置されています。
- エジェクタピン(押出機構)
成形品を金型から取り出す役割を果たします。
金型設計のポイント
インサート成形用の金型設計において重要なポイントは以下のようなものがあります。
- インサートの固定精度
インサート成形において、インサート部品の位置精度は大変重要です。わずかなズレが製品の品質や性能に対して大きく影響することが想定されます。固定方法の工夫としては、専用の固定ピン、治具を樹脂の流れに影響が出ない位置に適切に配置すること、磁石を用いて、金属部品を固定すること、より小型で精密なインサート部品の場合には、真空吸着による固定を用いることで部品のズレを防ぐことが挙げられます。また、樹脂を射出する際に、インサート部品を押し動かす可能性があるため、金型内の設計で圧力が均等に分散するように配置し、固定力を維持できるよう設計することも必要となります。
- 樹脂の流動設計
樹脂の流動が不均一の場合、欠陥が発生する可能性があるため適切にゲートの位置と数を設計する必要があります。また、ランナーやゲートはできる限り短くすることで、樹脂の圧力損失を抑えながら均一な流動を確保します、また、成形時に金型に残った空気やガスが、気泡やボイドといった製品の欠陥の原因となる可能性があります。そのため、ガスベント(排気口)を適切に配置し、効率よくガスを排出する必要があります。パーティングライン(型の合わせ面)についても微細な隙間を設けることで、ガス抜きをサポートできる設計等の工夫が製品の品質に大きく左右します。
- 離脱性
製品の形状や樹脂の特性に合わせてエジェクタピンをピン跡が残らないよう表面や外観部分を避けて配置し、製品の取り出しがスムーズに行えるようにします。また、製品が金型に張り付くことを防ぐため、金型には適度な抜き勾配(0.5度以上)を設けることも重要となります。製品形状がより複雑な場合には、特に配慮した勾配設計が必要となります。
- 耐久性及びメンテナンス性
金型は繰り返し使用することが前提となるため、耐久性とメンテナンス性の両方が求められます。そのため、SKD61等の耐摩耗性や耐熱性に優れた焼き入れ焼き戻し鋼を使用することが一般的になります。また、必要に応じて蒸着によって皮膜を形成するイオンプレーティングなどの高い硬度の表面コーティングを用いることがあります。また、エジェクタピンやゲート周辺など摩耗しやすい部品については交換しやすいように設計する必要があります。合わせて、定期的な清掃や修理がしやすいよう分解・組立が容易な設計も設計者に求められる工夫となります。
インサート成形における金型設計は、製品の品質向上、工程効率化、耐久性確保に直結する重要な要素となります。前述のポイントを初め多角的な視点から設計を行うことで、安定した生産が可能となります。
インサート成形で生じる欠陥・不良
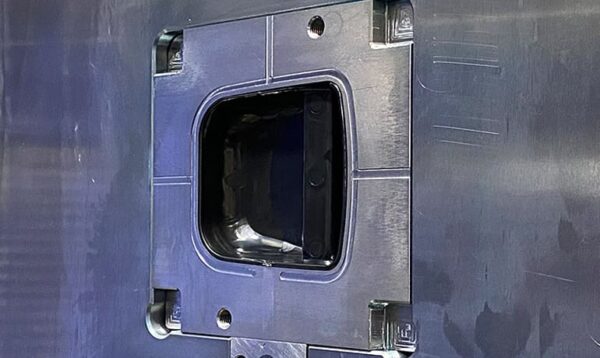
インサート成形は、金属部品などの異素材を金型内に配置し、その周囲にプラスチックを射出して一体化させる成形方法です。この技術は、製品の機能性や強度を向上させる一方で、特有の欠陥や不良が発生する可能性があります。以下に、主な欠陥とその原因について説明し、対策方法に関しては簡易的に説明する形式とし、また別の記事で詳しく紹介したいと思います。
キャビとられ
キャビとられとは、成形品が金型のキャビティ(固定側金型)に強く付着してしまい、取り出すことが困難となる現象です。本章の見出しのイメージに、他社サイト様でわかりやすい画像があるので、引用をさせて頂きましたので、ご参照ください。通常、成形品は可動側金型のコアに付着し、エジェクタピン(成形品を押し出すためのピン)で取り出されますが、キャビとられが発生すると生産効率が低下し、製品に傷が付くリスクも高まります。
キャビとられの発生原因としては、代表的なものとして以下の3つが挙げられます。
- 金型の抜き勾配(成形品が金型から離れやすくするための傾斜角度)が不適切である場合
- 金型表面の粗さが強い場合や傷がある場合
- 成形条件(射出圧力や温度)の不適切である場合
キャビとられは射出成形を行っている弊社でも、少なくはない不良の一つで、加工者のノウハウによる対策を施すことで、防ぐことが可能です。しかし、対策方法の説明は少し複雑となるため、また別の記事で改めて紹介する予定です。
ボイド(気泡)の発生
ボイドとは、射出成形により成形された製品の内部に空洞や気泡が生じてしまうことです。製品の外観不良の原因になることもあれば、外観検査のみでは検出しきれない場合もあり、製品の強度低下・破損の原因にまで発展してしまう場合もあります。
ボイドの発生原因としては、以下のようなものが考えられます。
- 射出速度が速すぎるため、樹脂内に空気が巻き込まれてしまう。
- 金型内のガス抜き(ベント)が不十分
- 樹脂の乾燥不足や湿気の混入 樹脂材料の管理の不十分
先ほども説明した通り、ボイドは外観検査だけで見つからない可能性もある非常にやっかいな不良の一つです。対策およびボイドの発生を検出するための検査方法については、また別の記事にて詳しく説明いたします。
ショートショット
ショートショットとは、樹脂が十分に充填されていなかったため、金型の隅々まで行き渡らず、製品の一部が欠けてしまうなど、未完成の状態になる不良です。主な発生原因は以下の通りです。
- 樹脂材料の充填不足
- 射出圧力や速度の不足
- 金型内の空気が適切に逃げない(ベント不足)
- 樹脂の温度が低すぎる
ショートショットは、射出成形・インサート成形においても、最も発生頻度が高い不良と言えるかもしれません。製品に欠けが生じてしまうため、求める機能・性能・強度を満たすことができないため不良となり、一般に手直しすることも困難です。対策方法は他にもございますが、材料の充填不足などは特に簡単に防げるため気を付けましょう。詳しい対策方法はまた別の記事にて、紹介したいと思います。
バリの発生
バリ(フラッシュと呼ばれる場合もある)は、最終製品の形状として不必要な樹脂がはみ出してしまう不良で、特に、人体には触れる製品では安全性の問題にもなります。
主な原因は以下が挙げられます。
- 金型の合わせ面の隙間の発生
- 射出圧力が高すぎる(射出圧力が高いため、すき間から樹脂がはみ出して、薄い膜状のバリが発生)
- 金型の摩耗、劣化
バリの対策は、上記の発生原因からも推測も容易かと思いますが、一般にインサート成形・プレスによる大量量産では、金型のメンテナンスや製作時の精度の担保は非常に重要な要素です。一方で、バリに関しては、外観検査での検出も容易で、手直し加工が行える場合も多い不良となります。弊社では、組立/検査ラインの構築と作業効率化に向けた改善を続けており、バリが発生した製品に関しても製品に求められる品質や強度・美観にもよりますが、バリ取りを行えるツールも豊富に取り揃えております。したがって、バリ発生の低減に関しても積極的に取り組んでおりますが、バリが発生した製品をお客様に納めることはございませんので、ご安心ください。
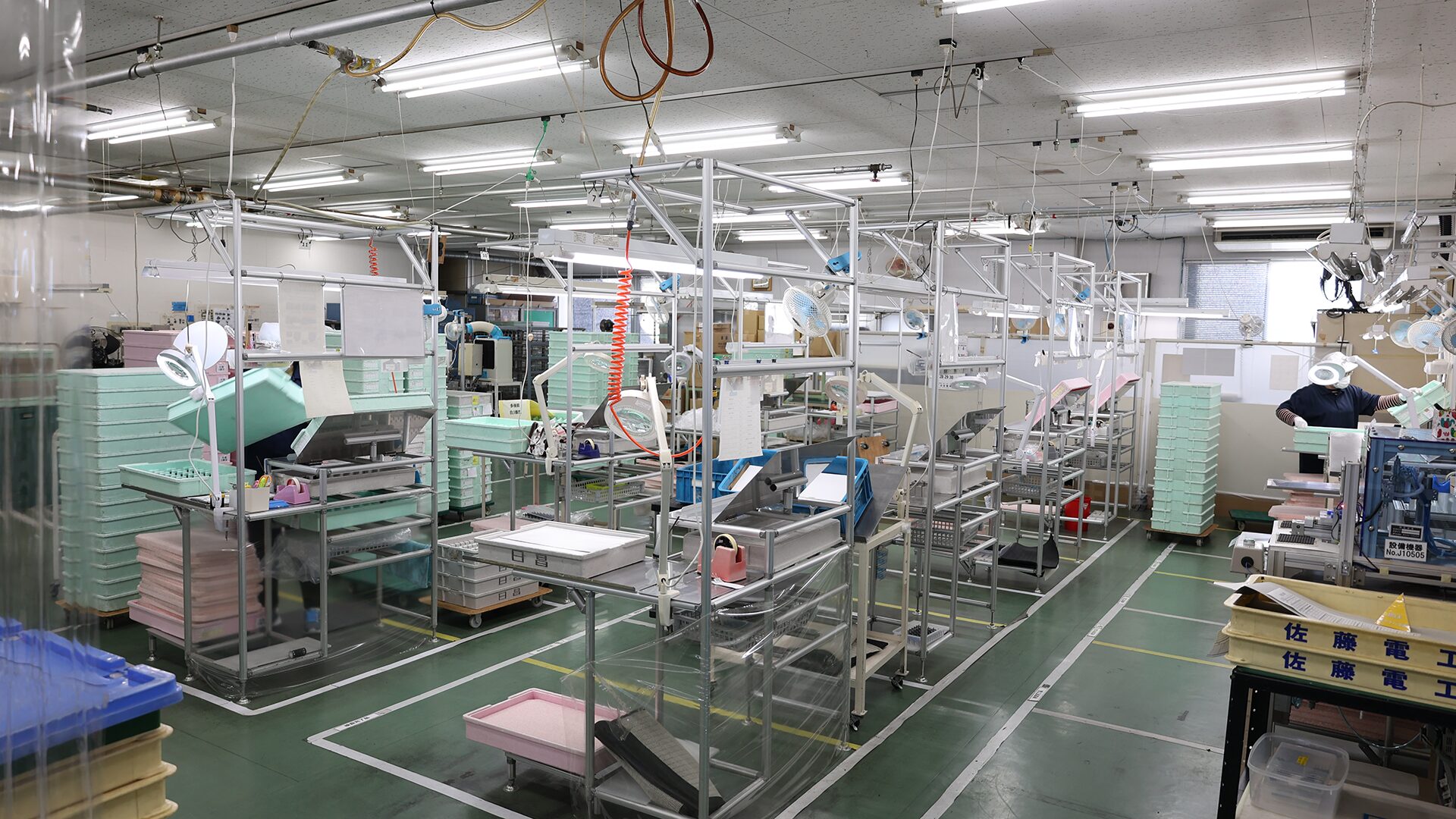
弊社の組立/検査ライン 弊社代表の製造ライン設計の経験ノウハウを活かして、
作業者一人ひとりにカスタマイズした業務効率化を目指す改善を日々行っております。
ウェルドライン
ウェルドラインとは、溶融樹脂が金型内で合流する際にできる線状の痕跡で、強度低下や外観不良の原因となります。原因としては以下が挙げられます。
- インサート部品の周囲で樹脂の流れが分岐・合流する際に発生
- 射出速度や温度が不適切で、樹脂の融合が不完全となってしまう
このウェルドラインの検出に関しては、一般に外観検査でクリアできますが、透明な樹脂を用いた製品や、必要に応じて、成形品の表面加工を(細かい模様やざらつきをつける加工)を行う場合もあり、不適切な検査を行ってしまうと見逃しも起きる可能性がある不良となります。
反り・歪み
射出成形では高熱の発生を伴う加工でもあるため、反りや歪みは比較的起こりやすい不良の一つです。製品に反りや歪みが発生してしまうと、寸法精度が低下し、組み立て不良の原因となります。少し、熱が原因になることについて述べてしまいましたが、主な発生原因は以下の通りです。
- インサート部品と樹脂の収縮率の差異
- 冷却速度の不均一
- 金型内の温度分布の不均一
ここで、反りや歪みに関しては、インサート成形でよく起きやすい不良でもあるため、対策法にも少し触れてみます。反りや歪みを抑えるためには、やはり、製品形状や金型形状を考慮した射出成形加工時の温度を適切に保てるかを予想する加工者や管理者のノウハウが重要です。また、樹脂材料の特性への深い理解も重要で、特に、近年ではCFRTP(カーボンファイバー強化熱可塑性樹脂)など、軽量化と強度の確保を両立する新素材も登場しており、定期的な知見のアップデートも求められます。
弊社もインサート成形の専門性・ノウハウの蓄積を続けておりますが、引き合いに関する相談で最終製品の形状、材料、使用する金型の設計内容をお伺いした際に、あらかじめ反りや歪みの発生は予想できる場合もあります。そこで、一点、下記の自社製品を紹介します。これは、自動車内部で利用される部品で、薄肉形状であることや使用材料の特性などからヒケ(成形品の表面が凹んでしまう現象、ここでは反り・歪みの一種として捉えます)の発生が予想できたため、リブ(補強材)の追加を提案し、実際に品質向上を実現することができました。(画像内部では、最下部に見える銀色の円筒状部品がリブとなります)したがって、反りや歪みの対策に関しては、必要に応じて設計変更まで行うことも一つの手です。
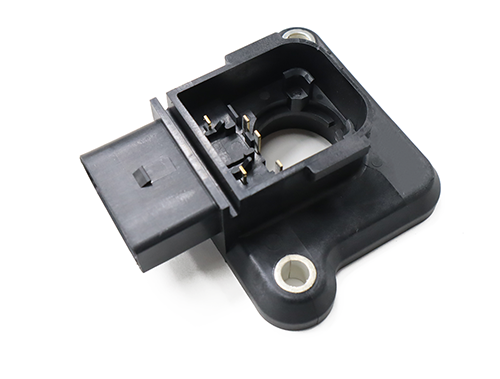
弊社が制作した自動車業界向け射出成形品 表面にへこみが発生する懸念があったため、部品にリブ(補強材)の追加を弊社から設計提案した製品
インサート部品の位置ずれ
インサート部品が所定の位置からずれると、製品の機能不全や外観不良を引き起こします。
主な原因は以下の2つが挙げられます。
- インサート部品の固定が不十分
- 射出時の樹脂圧力で部品が移動
インサート成形の実績が多い会社では、比較的強く注意を向けている不良であると弊社は考えていて、対策も十分に行っている会社も多いと思いますが、この不良に限った話ではないですが、短納期への対応や、作業者の心身の健康状態など、外的要因によって起こってしまうことも多いミスであると弊社は考えています。したがって、案件・納期の管理や監督者の設置や作業者同士のフォローが可能な体制の構築等も重要な施策であると考えております。
インサート成形に用いられる金型とは?まとめ
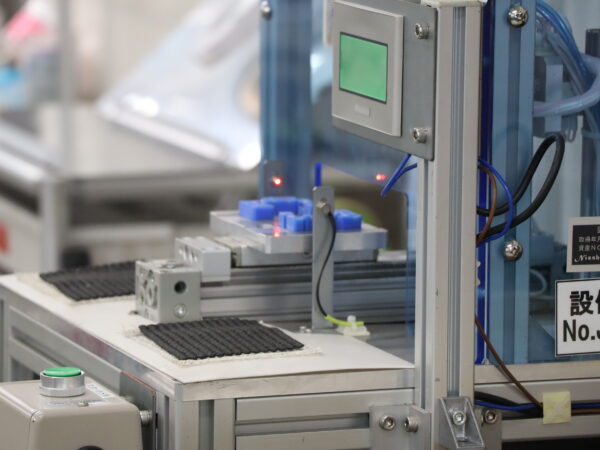
今回の記事では、インサート成形の加工技術および金型に関する基礎知識や、不良の発生原因などについて、解説しました。
インサート成形は、金属と樹脂などの異なる材料を一体化させて製品を成形する技術であり、それに伴い、複数の性質が異なる材料も使用することにも起因して、他の部品加工で注意すべきポイントとはまた少し毛色も異なるポイントが多く含まれます。
また、今後追加する記事では、インサート成形で発生する不良の対策に関しても、より具体的に説明させて頂く予定となっておりますので、もしご興味を持っていただけましたら、引き続き弊社のコンテンツのチェックを行っていただけますと幸いです。
根本電工株式会社では、射出成形加工による部品の量産を事業の柱の一つとしており、最近ではEV業界など、新素材を利用する部品の製造などにおいても高品質な製品の提供を行っております。もし、インサート成形を要する部品の製造に関するお困りごとがございましたら、技術に関するご質問も歓迎いたしますので、お気軽に弊社までご相談ください。
ここまで読んでいただき、ありがとうございました。次回の記事更新についても今しばらくお待ちください。

お問い合わせ
Contact
技術的なご相談からお見積りの依頼まで
お気軽にご相談ください。
メールでのお問い合わせはコチラ
お電話でのお問い合わせはコチラ
(0293)24-0567
営業時間:8:00~17:00
お問い合わせ
Contact
技術的なご相談から
お見積りの依頼まで
お気軽にご相談ください。
メールでのお問い合わせはコチラ
お電話でのお問い合わせはコチラ
(0293)24-0567
営業時間:8:00~17:00