射出成形機とは?構造・種類・竪型と横型の違いを徹底解説!
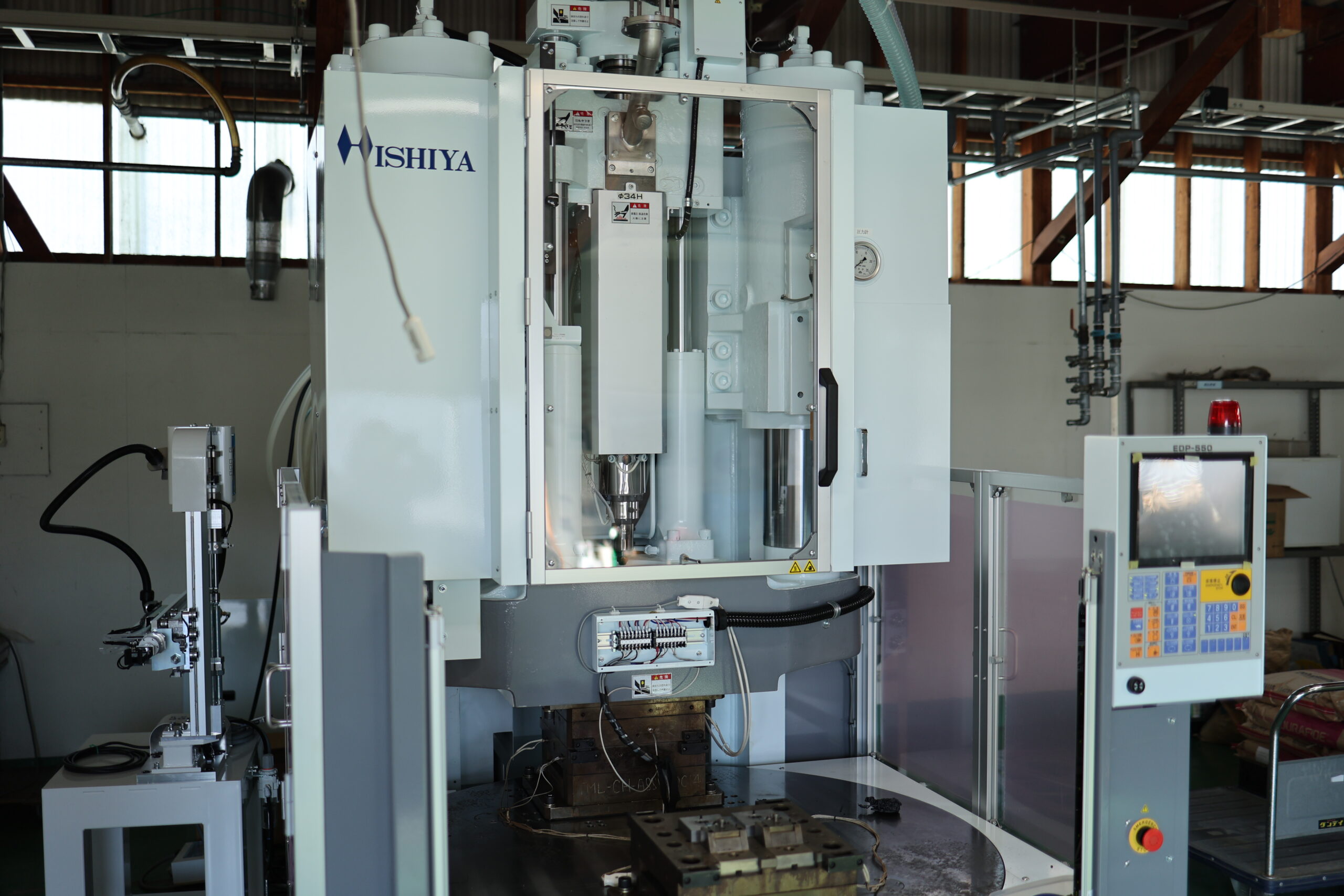
プラスチック製品の製造において欠かせない存在が射出成形機です。自動車部品や日用品、医療機器に至るまで、幅広い分野で使用されているこの装置は、樹脂を溶かし、金型へ射出して成形することで、高精度な製品を大量に生産できます。しかし、一口に射出成型機といっても、電動式や油圧式、竪型成形機や横型成形機など、さまざまな種類があり、それぞれの特性を理解することが重要です。
特に、「竪型成形機」と「横型成形機」は、射出成形の代表的なタイプであり、構造や特性、用途に応じたメリット・デメリットが異なります。
本記事では、射出成形機の基本的な仕組みや構造から、竪型成形機と横型成形機の違い、特徴、そして用途ごとにどちらを選ぶべきかについて詳しく解説します。
射出成形機とは?
射出成形機は、プラスチック製品を製造するための成形機械の一種であり、樹脂を加熱して溶融させ、金型に高圧で射出・充填し、冷却・固化することで成形品を作り出します。この成形方法は、大量生産が求められる工業製品から、精密機械部品まで幅広く対応できるため、現代の製造業において欠かせない技術 です。
射出成形機の構造は、大きく分けて 「射出ユニット」 と 「型締ユニット」 の2つで構成されています。射出ユニットでは 樹脂を加熱・溶融し、金型内へ射出する 役割を担います。一方、型締ユニットは、金型を強固に固定し、成形中の圧力に耐えながら正確な形状を作り出す 役割を果たします。この2つのユニットが連携することで、寸法精度の高い製品を安定して成形できる仕組みになっています。
また、射出成形機は 生産効率やコスト削減の面でも優れた特性 を持っています。たとえば、スマートフォンのケースや自動車部品、家電製品、さらには医療機器や食品容器など、私たちの身近な多くの製品が、この技術によって製造されています。 多品種・大量生産に適した成形技術として、幅広い分野で活用されています。
射出成形機での成形の流れ
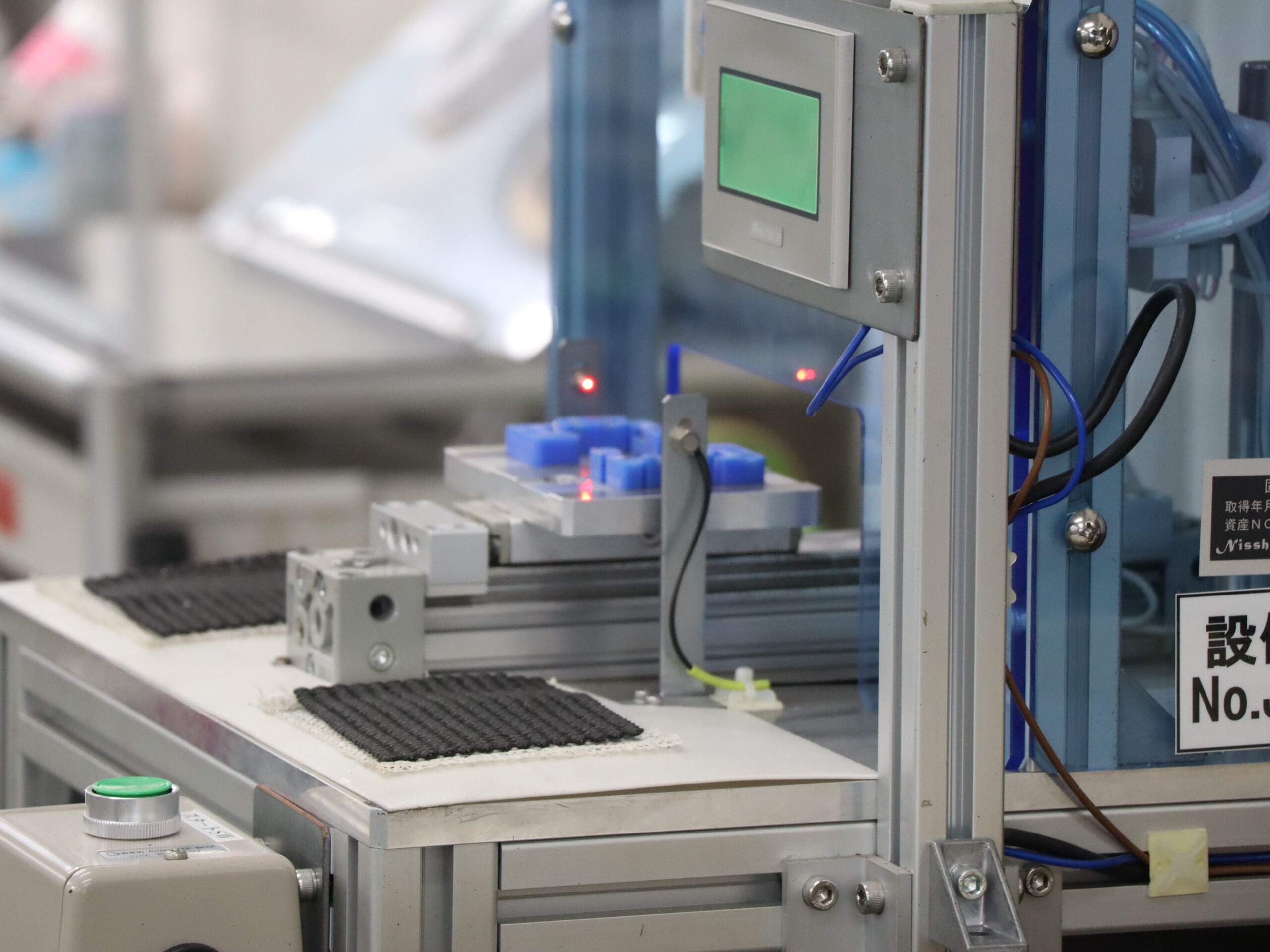
射出成形は、プラスチック製品を製造するために、樹脂を加熱・溶融し、金型へ射出・充填し、冷却・固化させる一連の工程 です。これらの作業を適切に管理することで、高品質な製品を効率的に生産することが可能 になります。
射出成形の工程は、大きく 「溶融」「充填」「固化」 の3つの段階に分けられ、それぞれの工程が成形品の品質に大きな影響を与えます。
ここでは、それぞれの工程について、詳しく解説します。
溶融(ようゆう)
溶融は、成形材料(プラスチック樹脂)を適切に加熱し、次の充填工程に供給するための準備を整える重要な作業です。
まず、ペレット状の成形材料がホッパー(供給装置)に投入され、重力によってスクリューシリンダー内部へ送られます。 このスクリューは回転しながら材料を前方へ押し出し、同時に圧縮していきます。圧縮によって材料同士が密着し、加熱が効率よく行われるようになります。
加熱はシリンダーに装着されたバンドヒーターの熱と、スクリューの回転による摩擦熱を組み合わせて行われます。 これにより、材料が均一に溶融し、適切な流動性を持つようになります。
さらに、溶融した材料はスクリュー内で圧縮されながら混練されます。この混練によって 樹脂の粘度が均一化され、内部の気泡や異物が除去されるため、成形品の品質向上につながります。 最終的に、溶融された材料はスクリューの先端に蓄積され、次の充填工程へと進みます。
溶融工程では、樹脂温度の管理が重要 です。温度が高すぎると樹脂が分解し、製品に欠陥が生じる可能性があります。一方、温度が低すぎると十分に溶融せず、流動性が不足して成形不良につながります。そのため、加熱シリンダーの温度設定やスクリューの設計が成形品質を左右します。
充填(じゅうてん)
充填は、溶融した樹脂を金型のキャビティ内に均一に流し込む工程です。この工程は、成形品の形状や品質を決定づける重要なステップであり、射出速度や圧力、金型の設計が大きく影響を与えます。
まず、型閉じと型締めが行われます。この段階では、金型が強い力で密着され、樹脂の射出時に金型が開かないようにします。型締めは、キャビティ内に正確な形状を作るために非常に重要な工程で、直圧式やトグル式といった型締ユニットの仕組みを使用します。
その後、スクリューの先端に蓄えられた溶融樹脂がノズルを通じて金型に送り込まれます。この射出動作は、スクリューが前進することによって行われ、溶融樹脂は高圧で押し出されながらキャビティ内に流れ込みます。射出速度と圧力の調整は非常に重要で、過度な速度や圧力はキャビティ内での乱流を引き起こし、製品の欠陥につながる可能性があります。一方で、低すぎるとキャビティの隅々まで樹脂が行き渡らず、欠けや寸法不良が発生するリスクがあります。
充填が進むと、溶融樹脂は金型内で一定のパターンに沿って広がり、キャビティの形状を満たしていきます。このとき、金型内の通気経路(ガスベント)が適切に設けられていることで、樹脂の流れを妨げる空気が排出され、充填がスムーズに行われます。また、充填が完了する際には、樹脂が収縮して形状が不完全になるのを防ぐために、保圧がかけられます。
充填工程は、成形品の外観や寸法精度に直接影響を与えるため、射出条件の最適化が求められます。金型温度、樹脂温度、射出速度、保圧力など、多くの要因が絡み合うため、これらを適切に制御することが製品の品質向上につながります。この工程を経て、成形品は次の工程である「固化」の準備が整います。
固化(こか)
固化は、射出された溶融樹脂が金型内で冷却されて固まる工程です。この工程は、製品の最終的な形状と品質を決定する重要な段階です。適切な冷却と型開きのタイミングが、成形品の寸法精度や外観品質に大きく影響を与えます。
射出された溶融樹脂は、金型内のキャビティを満たした後、金型の冷却機能によって徐々に温度を下げて固化します。金型には冷却水が通る冷却回路が設けられており、これが効率的に熱を奪うことで、溶融樹脂が短時間で固化します。この冷却速度は成形品の品質に大きく影響を与えるため、冷却水の流量や温度を適切に調整する必要があります。
冷却が完了すると、型開き工程に移ります。この段階では、金型が慎重に開かれ、成形品が金型から取り外されます。型開きの際には、成形品が金型に引っ付かないように設計された抜き勾配や、押出しロッドが使用されます。この押出しロッドは、金型内部にある成形品を押し出して取り外すための機構です。
固化工程の適切な管理は、成形品の寸法精度や機械的特性を確保する上で重要です。冷却が不十分な場合、成形品の表面に欠陥が生じたり、寸法のばらつきが発生する可能性があります。一方で、冷却時間が長すぎると生産効率が低下するため、最適な冷却条件を見極めることが必要です。
このようにして、固化工程を通じて完成した成形品は、最終的に金型から取り外され、次の工程へと進みます。この段階が、射出成形の全工程を締めくくる重要なステップとなります
射出成形機の構造
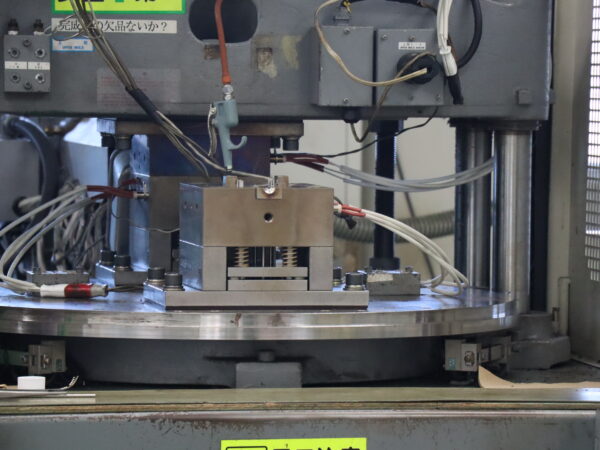
射出成形機の構造は、製品の品質や成形プロセスの効率性を大きく左右する重要な要素です。この機械は複数のユニットで構成され、それぞれが特定の役割を果たしながら、成形工程全体を支えています。主に「射出ユニット」「型締ユニット」「コントローラー」の3つの主要な構造から成り、これらが一体となって機械の動作を制御し、高精度な成形を実現します。
ここでは、各ユニットの役割とその仕組みについて詳しく解説します。
射出ユニット
射出ユニットは、射出成形機の中でも最も重要な役割を担う部分の一つであり、成形材料を加熱・溶融し、適切な圧力で金型へ射出する役割を果たします。そのため、成形品の品質や生産効率に大きな影響を及ぼします。
このユニットには、「プランジャー式」「プリプラ式」「スクリュー式」の三つの方式があり、それぞれに異なる構造や特徴があります。
- プランジャー式
プランジャー式射出ユニットは、1960年代初頭まで主流であった射出方式で、現在では特殊な用途に限って使用されています。この方式では、ホッパーから供給された成形材料が加熱シリンダー内に落下し、ピストン型のプランジャーによって圧力をかけられながら射出されます。射出の過程では、加熱シリンダー内で材料が溶融され、均一な流動を確保するために「トーピード」と呼ばれる部品を通過します。このトーピードは、魚雷に形が似ていることからその名前がつけられています。
ホッパー内の材料は自重で落下し、計量器を介して一定量が供給されます。その後、プランジャーが前進することで加熱シリンダー内の材料を溶融しながら押し出し、金型へと流れ込みます。シンプルな構造であるため、メンテナンスが容易で製造コストが比較的安価であるという特徴があります。
この方式のメリットとして、シンプルな構造のためメンテナンスが容易であり、製造コストが比較的安価である点 が挙げられます。
しかし、材料の溶融が不均一になりやすいため、成形品の品質が安定しにくい という課題があります。また、高精度な射出が難しく、複雑な形状や厳しい品質が求められる成形には適していません。そのため、現在では特殊用途や試作工程でのみ使用されることがほとんどです。
- プリプラ式
プリプラ式射出ユニットは、2本のシリンダーを組み合わせた構造を持つ特殊な射出方式で、成形材料の予備可塑化と射出を別々のシリンダーで行います。この方式では、成形材料を効率的に溶融し、精度の高い射出を可能にするために、「プリプラ用加熱シリンダー」と「射出用加熱シリンダー」の2つのシリンダーが使用されます。
まず、ホッパーから供給された成形材料はプリプラ用加熱シリンダー内で加熱され、溶融されます。この予備可塑化工程により、材料が射出に最適な状態に整えられます。次に、溶融された材料は射出用加熱シリンダーに送り込まれ、射出プランジャーによって金型内に高精度で射出されます。
プリプラ式射出ユニットはさらに、「プランジャープリプラ式」と「スクリュープリプラ式」の2種類に分類されます。
- プランジャープリプラ式
プランジャープリプラ式は、予備可塑化にプランジャーを用いたシンプルな構造を採用しており、成形材料を効率的に溶融することが可能です。この方式では、プランジャーが加熱されたシリンダー内で成形材料を押し出し、均一な溶融を実現します。溶融された材料は射出用加熱シリンダーに送り込まれ、さらに射出プランジャーによって金型内に精密に射出されます。
構造がシンプルなためメンテナンスが容易で、安定した射出成形を行える のが特徴ですが、材料の混練(かき混ぜ)が不十分になる場合があり、複雑な形状や高い均一性が求められる製品の成形にはやや適さない という課題もあります。それでも、特定の用途や簡易的な成形では現在でも一定の需要がある方式です。
- スクリュープリプラ式
スクリュープリプラ式は、予備可塑化にスクリューを使用する構造で、材料の均一な混練と溶融を可能にする点が大きな特徴です。この方式では、スクリューの回転によるせん断熱効果と加熱シリンダー内の熱で、成形材料が効率的に溶融されます。溶融された材料は射出用加熱シリンダーに送られ、射出プランジャーによって精密に金型内へ射出されます。
スクリュープリプラ式の最大のメリットは、材料の均一性が高く、複雑な形状や高品質が求められる製品の成形にも適している点です。また、射出中に次ショット分の材料の可塑化を同時に行うことができるため、高効率なハイサイクル成形が可能です。ただし、構造が複雑であるため、材料交換が手間であり、特に熱分解を起こしやすい樹脂の成形には向いていないというデメリットがあります。
- スクリュー式
スクリュー式射出ユニットは、現在の射出成形機の中で最も広く採用されている方式です。このユニットでは、1本のスクリューが「可塑化」「混練」「計量」「射出」の全工程を担う仕組みになっています。スクリューが回転しながら材料を前進させることで、均一な混練と効率的な溶融が実現します。
ホッパーから投入されたペレット状の材料は、シリンダー内をスクリューによって移動しながら、外部のバンドヒーターやスクリュー回転によるせん断熱で溶融されます。溶融した材料はスクリュー先端に蓄えられ、一定量が蓄積されるとスクリューが前進し、金型内へ高精度に射出されます。この一連の流れにより、材料の均一な溶融と精密な射出が可能になります。
スクリュー式の最大のメリットは、材料の混練が均一であることです。これにより、成形品の品質が高まり、複雑な形状や薄肉部品の成形にも対応可能です。また、スクリューの設計を工夫することで、さまざまな樹脂に適応できる汎用性の高さも特徴です。
一方、スクリュー式のデメリットとしては、構造が複雑であるため初期コストが高くなることや、メンテナンスの手間がかかる点が挙げられます。しかし、その多機能性と高精度な成形能力から、現在では多くの産業で標準的な選択肢として用いられています。
スクリュー式射出ユニットは、現代の射出成形技術を支える中核的な装置として、その信頼性と性能が広く評価されています。
型締ユニット
型締ユニットは、射出成形機において成形工程を支える重要な部分で、金型を固定し、射出された樹脂がキャビティ内で適切に成形されるための力を提供します。この画像に示されているように、型締ユニットは「型締シリンダー」「可動側ダイプレート」「固定側ダイプレート」「タイバー」などで構成されています。
型締シリンダーは、油圧や電動モーターを使用して金型を締め付ける力を発生させます。この力は射出工程中の高い内圧に耐えるために不可欠で、成形品の寸法精度や品質に大きな影響を与えます。可動側ダイプレートは型締シリンダーの動きによって金型を開閉させる部分で、製品を取り出す際に重要な役割を果たします。一方、固定側ダイプレートは金型をしっかりと固定し、安定した成形工程を実現します。
また、画像中のタイバーは、型締時の反力を受け止め、ユニット全体の強度と安定性を維持します。この設計により、高い型締力を効率的に支えることが可能となります。
型締ユニットの機能は成形品の品質や生産効率に直結しており、特に高精度な製品や複雑な形状の成形において、その重要性が際立ちます。次のセクションでは、この型締ユニットの種類について詳しく解説します。
- 直圧式
直圧式は、型締シリンダーを用いて油圧を直接利用し、金型を締め付ける方式 です。この画像に示されているように、型締シリンダーが型締ラムを前後に動かし、金型をしっかりと固定する構造 になっています。このシンプルな構造が直圧式の大きな特徴であり、高い型締精度を実現するとともに、メンテナンスの容易さ にも優れています。
直圧式の最大の利点は、型締力を直接シリンダーで制御することができる点です。
これにより、設定した圧力を精密に再現しやすく、精密部品の成形や高い寸法精度を求める製品の製造に適しています。 また、型締力が均一に伝わりやすい構造 であるため、成形品全体の品質が安定しやすく、成形ムラを抑える効果も期待できます。
しかし、直圧式にはいくつかの課題もあります。型締力は油圧シリンダーの能力に依存するため、大型の成形機や非常に高い型締力が必要な場合には、油圧装置が大型化してしまう 傾向があります。そのため、直圧式は特に小型から中型の射出成形機でよく採用される方式 です。
直圧式型締ユニットは、シンプルな構造と精密な制御性能を兼ね備えており、安定した成形を求める製造環境に適した方式 です。
- トグル式
トグル式は、型締シリンダーの動力を「トグルリンク機構」に伝達し、型締力を生み出す方式 です。この方式の特徴は、トグルリンクの力学的効果を利用して少ないエネルギーで高い型締力を実現できる点にあります。この画像に示すように、トグルリンクが型締時に直線状に伸びることで、大きな締め付け力を効率よく発生させます。
トグルリンクの動作により、型締と型開きの速度が速くなるため、生産効率の向上に貢献します。また、エネルギー消費が抑えられる省エネルギー設計であることから、大量生産における使用に適しています。さらに、リンク機構の動作が比較的スムーズであるため、成形サイクルを短縮することが可能です。
特に、トグルリンク機構を採用することで、型締力を効率よく増幅できるため、電動式射出成形機では主にトグル式が採用 されることが多いです。
一方で、トグル式にはいくつかの課題もあります。
トグルリンク部は摩耗や変形が発生すると型締力の低下を招く可能性があるため、定期的なメンテナンスが必要 です。また、型締力がリンクの動作位置によって変動するため、細かい調整が難しい というデメリットもあります。
トグル式型締ユニットは、高速動作や省エネルギーが求められる大量生産向けの成形機に広く採用されており、中型から大型の射出成形機で特に活用されています。
コントローラー
コントローラーは、射出成形機の動作を管理し、成形工程全体を制御する重要な装置 です。射出速度や温度、射出量、型締力、冷却時間などの成形条件を正確に管理することで、安定した製品品質の維持と生産効率の向上を実現 します。コントローラーの性能は成形機の精度や生産性に直接影響を及ぼすため、射出成形機における「頭脳」ともいえる重要な要素です。
コントローラーには内蔵型と外付け型の2種類があり、機種や用途に応じて使い分けられます。内蔵型コントローラーは、成形機本体と一体化しているため、操作性や管理性に優れています。一方、外付け型コントローラーは柔軟性が高く、複数の成形機を統一的に制御したり、特定の作業環境に応じて配置を変更することが可能です。
近年の射出成形機には、デジタル技術を活用した高機能なコントローラーが搭載されており、タッチパネルやグラフィカルなインターフェースを採用することで、直感的な操作が可能 になっています。さらに、設定した成形条件を保存・呼び出しする機能があるため、製品ごとの再現性を確保しやすくなっています。
また、IoTやAI技術の発展により、コントローラーはさらなる進化を遂げています。
成形機の稼働状況やエラー情報をリアルタイムで監視し、遠隔操作や予知保全が可能 となっています。これにより、生産ラインの効率化やトラブル発生時の迅速な対応が可能となり、ダウンタイムの削減 に貢献しています。
コントローラーの適切な運用と管理は、成形品質の向上と生産性の最適化につながる ため、最新技術を活用した精密な制御が求められます。
射出成形機の種類
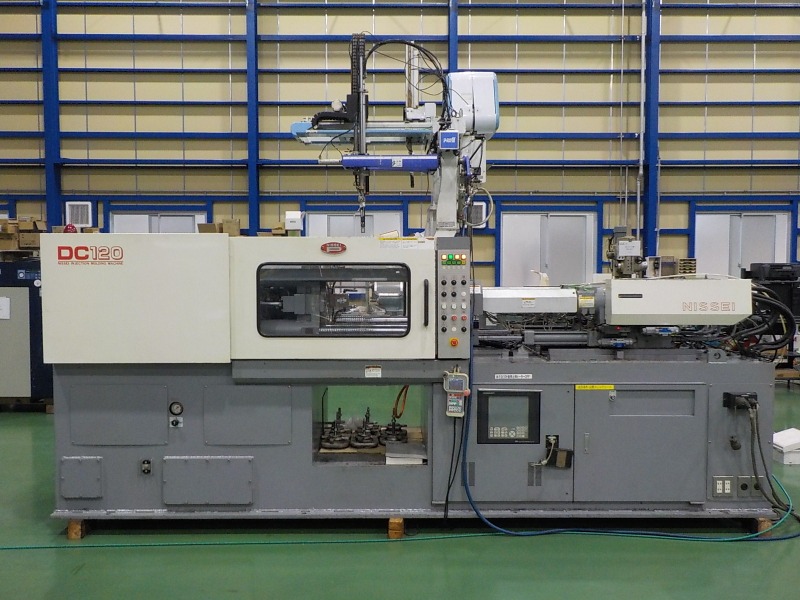
射出成形機には、主に 「電動式射出成形機」 と 「油圧式射出成形機」 の2つのタイプが存在します。どちらも樹脂を溶融し、金型へ射出・充填して成形するという基本的な仕組みは共通していますが、それぞれの駆動方式や構造、性能には大きな違いがあります。
電動式射出成形機 は、サーボモーターを用いて射出や型締を制御する方式 であり、省エネルギー性や高精度な成形が可能 な点が特徴です。一方、油圧式射出成形機 は、油圧の力を利用して動作する方式 で、高い射出圧力と耐久性に優れ、大型成形や厚肉成形に適しています。
成形機の選択は、製造する製品の種類や生産条件、コスト によって決まります。例えば、寸法精度が求められる精密成形やクリーンな環境が必要な医療・食品業界では電動式が選ばれやすく、大型製品や高圧成形が必要な工業製品では油圧式が適している ことが多いです。
それぞれの成形機には メリット・デメリットがあり、用途に応じて適切なものを選択することが、効率的かつ高品質な成形を実現するために重要 です。
ここでは、電動式射出成形機と油圧式射出成形機の構造や特徴、メリットとデメリットについて詳しく解説します。
電動式射出成形機
電動式射出成形機は、射出成形に必要な動作をすべて サーボモーターで制御する方式 を採用しています。この技術により、速度・圧力・位置などを精密に管理できるため、成形品の寸法や品質を高いレベルで安定させることが可能 です。
また、電動式の型締め方式には 「トグル式」 と 「直圧式」 の2種類がありますが、特にトグル式 が広く用いられています。
- 電動式のメリット
電動式射出成形機の最大の利点は、高精度な成形が可能であること です。サーボモーターが射出装置を正確に制御することで、成形品の 寸法や形状を安定的に保つ ことができます。これにより、油圧式では実現が難しい、ミクロン単位の精度が求められる成形に適している という強みがあります。
また、電動式は 省エネルギー性能 にも優れており、必要な時に必要な分だけモーターを駆動させることで、従来の油圧式と比較して40%~50%の電力削減 が可能です。電気使用料の低減に加え、低騒音で作業環境を快適に保つ ことができるため、クリーンな工場環境の構築にも貢献します。
さらに、成形サイクルの短縮 も大きなメリットの一つです。電動式は 4つ以上の独立したモーターを搭載することで、複数の工程を並列で進行させることができる ため、生産性が向上します。短時間で大量生産が可能になり、コスト削減や納期短縮にもつながります。
環境面でも優れた特性を持ち、作動油を使用しないため、オイル漏れの心配がなく、衛生的 です。このため、食品容器や医療品など、クリーンな環境が求められる分野に適している だけでなく、冷却水の使用量が少なく、環境負荷の軽減にも貢献 します。
- 電動式のデメリット
一方で、電動式には 導入コストの高さ というデメリットがあります。サーボモーターを多く搭載しているため、機械本体の価格が油圧式と比較して高価 であり、初期投資が大きくなります。そのため、生産量や製品の特性に応じたコストバランスの検討が重要 となります。
また、電動式は 設定した条件に忠実に動作するため、急な調整や微妙な圧力変更には対応しにくい という特性があります。油圧式のように柔軟に圧力をコントロールできないため、成形条件の細かい調整が求められる工程では運用が難しい場合がある でしょう。
さらに、電動式は 操作や条件設定が複雑であり、導入時にオペレーターの習熟が必要 です。そのため、適切な知識と経験を持つ技術者が求められます。
電動式射出成形機は、高精度・省エネルギー・低騒音・環境負荷の低減といったメリット を備え、特に医療・食品・精密部品などの分野で広く活用されています。
しかし、導入コストや柔軟性の低さ、操作の難しさといった課題もあるため、用途や生産規模を考慮した上で選択することが重要 です。
油圧式射出成形機
油圧式射出成形機は、油圧の力を利用して射出や型締めを行う成形機 です。この方式は 「パスカルの原理」 を基にしており、作動油を介して圧力を金型や射出部に伝え、大きな力を発生させる仕組み になっています。主に 直圧式の型締め方式 が採用されており、高い型締力を発揮できる点が特徴です。
- 油圧式のメリット
油圧式射出成形機の最大のメリットは、高い圧力を安定的に発生できる点 です。油は圧縮性がほとんどないため、強い型締め力が必要な厚肉成形や大型成形品の製造に適して います。そのため、自動車部品や家電製品の外装部品など、大きなサイズや重量のある製品の成形 に効果を発揮します。
また、電動式と比較して導入コストが低い こともメリットの一つです。機械の構造が比較的シンプルであり、購入価格が安価 なため、初期投資を抑えて導入できます。さらに、油圧の圧力を調整することで、柔軟な成形条件の設定が可能 であり、材料や製品に応じた微調整がしやすい という利点もあります。
加えて、油圧式射出成形機は 力強い動作が可能であり、厚肉部品や複雑な形状の成形においても安定した結果を得られる ため、多くの産業で使用されています。
- 油圧式のデメリット
一方で、油圧式にはいくつかのデメリットもあります。電動式と比較してエネルギー消費量が多く、動作中の騒音も大きい ため、消費電力のコスト増加や作業環境への影響 が懸念されます。特に 夜間の生産やクリーンルームでの使用には適さない場合があります。
また、油圧の制御は細かい精度に限界があるため、成形品の寸法や形状の再現性が電動式ほど安定しません。このため、高精度な寸法管理が求められる製品の成形には不向き な場合があります。
さらに、作動油を使用することによるオイル漏れのリスク もデメリットの一つです。オイル漏れが発生すると機械の稼働が停止し、生産性が低下する可能性 があります。また、油は金属を脆化させる特性を持つため、油温や品質管理を徹底する必要 があり、定期的なメンテナンスが必須 となります。こうした維持管理の手間やランニングコストの増加 も考慮する必要があります。
油圧式射出成形機は、強力な型締め力を発揮し、大型製品や厚肉成形品の製造に適している ことが大きなメリットです。さらに、導入コストが比較的安価であり、柔軟な成形条件の設定が可能 という点でも利便性があります。
しかし、消費電力の高さや騒音、油漏れリスク、寸法精度の管理が難しいといった課題 もあるため、用途に応じた適切な選択が求められます。高精度な成形が求められる場合は電動式を、強い圧力が必要な成形では油圧式を選ぶなど、成形品の特性に応じた使い分けが重要 です。
射出成形機の分類
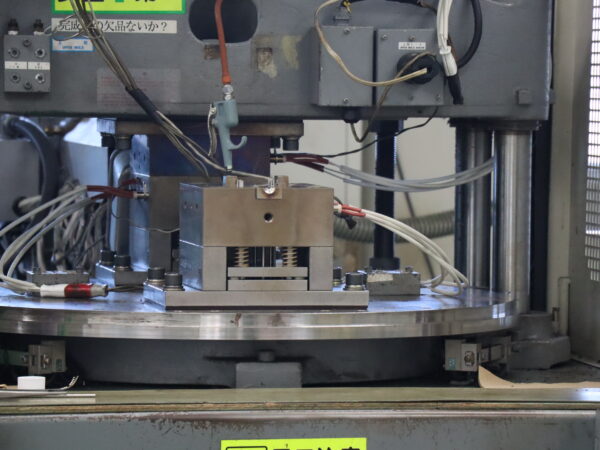
射出成形機は、射出装置と型締装置の組み合わせによって分類され、それぞれのタイプが異なる特性と用途を持っています。特に、竪型成形機と横型成形機の2種類 は、成形工程や設置環境、製品の要件に応じて選ばれます。この分類は、効率的な成形や生産性向上に直結するため、用途に応じた適切な選択が重要です。
ここでは、竪型成形機と横型成形機の構造や特徴について詳しく解説し、それぞれのメリットやデメリットを明らかにします。
竪型成形機(たてがた)
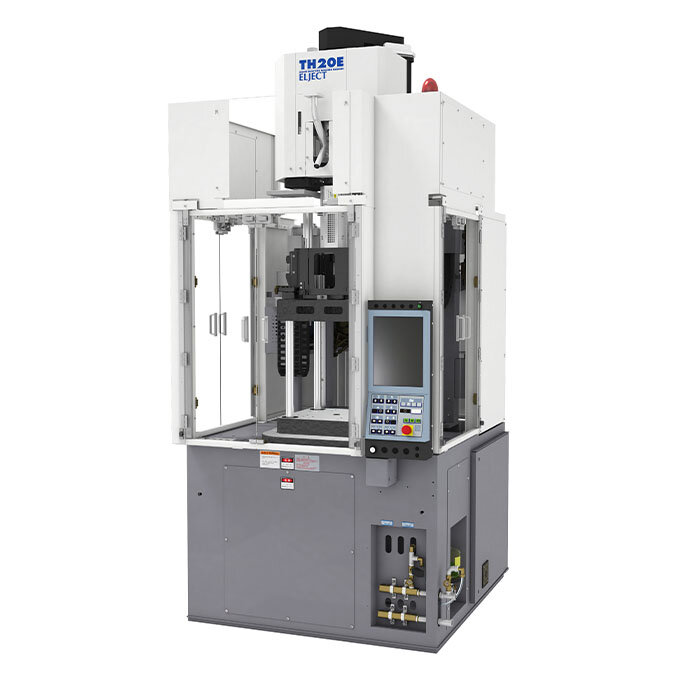
竪型成形機は、型締ユニットが垂直方向に動作する射出成形機 です。このタイプの成形機は、省スペース性とインサート成形への適応性が高い ことから、電子部品やコネクタの製造などで広く活用されています。竪型成形機では、金型が上下に開閉し、材料が上から流し込まれる構造になっているため、インサート材の配置がしやすく、作業効率が向上します。
また、竪型成形機は、多工程成形や自動化ラインとの組み合わせにも適しているため、工場の生産性向上に貢献します。特に、重力の影響を活用して樹脂が均一に流れることにより、成形不良を低減できる点も大きな利点です。しかし、金型の開閉時に高さ方向のスペースが必要になるため、設置環境によっては導入が難しい場合があります。また、成形できる製品サイズには制約があり、小型から中型の成形品の製造が主な用途となります。
- 竪型成形機の構造
竪型成形機は、射出ユニットと型締ユニットが垂直に配置されている のが特徴で、金型が上下方向に開閉する構造になっています。この設計により、インサート成形の際には、部品を安定して配置しやすく、手作業によるセットや自動化ラインとの連携がしやすくなっています。さらに、金型が閉じられた状態で部品が固定されるため、樹脂が均一に流れ込みやすく、成形品の精度が向上します。
また、竪型成形機は、クランプユニット(型締機構)、射出ユニット(樹脂を射出する装置)、コントロールユニット(温度や射出速度などを制御する装置) で構成されており、特にインサート成形に特化した機能を備えています。さらに、一部の竪型成形機ではロータリーテーブルやスライドテーブルを搭載することで、インサート成形後の次工程へスムーズに移行でき、成形サイクルの短縮や自動化の促進が可能です。
- 竪型成形機のメリット
竪型成形機の最大の利点は、インサート成形がしやすい 点にあります。金型が垂直方向に開閉するため、開いた状態でインサート材を正確に配置でき、手作業だけでなくロボットによる自動化にも適した構造 になっています。特に、金属部品を樹脂で包むような成形 には最適であり、製品精度の向上 に貢献します。
また、省スペース性も竪型成形機の大きな強みの一つ です。同じ型締力の設備で比較すると、横型成形機と比べて設置面積が小さい ため、工場のレイアウトが限られている場合でも導入しやすくなっています。さらに、重力を利用することで、樹脂が均等に流れやすく、寸法精度が求められる製品にも適している 点が特徴です。
さらに、竪型成形機は、多工程成形にも適している ため、ロータリーテーブルやスライドテーブルを備えたモデルでは、成形サイクルを短縮し、生産効率を大幅に向上させる ことが可能です。これにより、インサート成形後の次工程へのスムーズな移行が実現し、工場全体の生産性向上 に寄与します。
- 竪型成形機のデメリット
竪型成形機には多くの利点がありますが、いくつかの課題も存在します。まず、成形できる製品のサイズには制約があり、大型の成形品には適していません。金型が上下に開閉する構造上、大型の部品を扱うには高さ方向のスペースが不足 するため、小型から中型の成形品に限定される傾向があります。
また、設備コストが高くなる可能性 もあります。特に、ロータリーテーブルやスライドテーブルを搭載した高機能モデルでは、導入コストが高くなる ことがあり、工場の設備投資計画に影響を与えることがあります。さらに、竪型成形機ではオペレーターの作業位置が高くなるため、安全対策が必要 になるケースもあります。
成形品の取り出し方法についても、横型成形機とは異なる課題 があります。横型成形機では、成形品が自然に落下するため搬送が容易ですが、竪型成形機では製品が金型の下側に残るため、ロボットアームやスライドテーブルなどの取り出し装置を活用する必要 があります。これにより、自動化設備の追加コストやオペレーターの負担が増加する可能性 があります。
さらに、油圧を使用する竪型成形機の場合、エネルギー消費量が増加することがある ため、電動式の横型成形機と比較するとランニングコストが高くなる可能性 があります。これは、長時間の稼働時に特に影響を及ぼし、コスト管理の面で注意が必要 です。
横型射出成型機
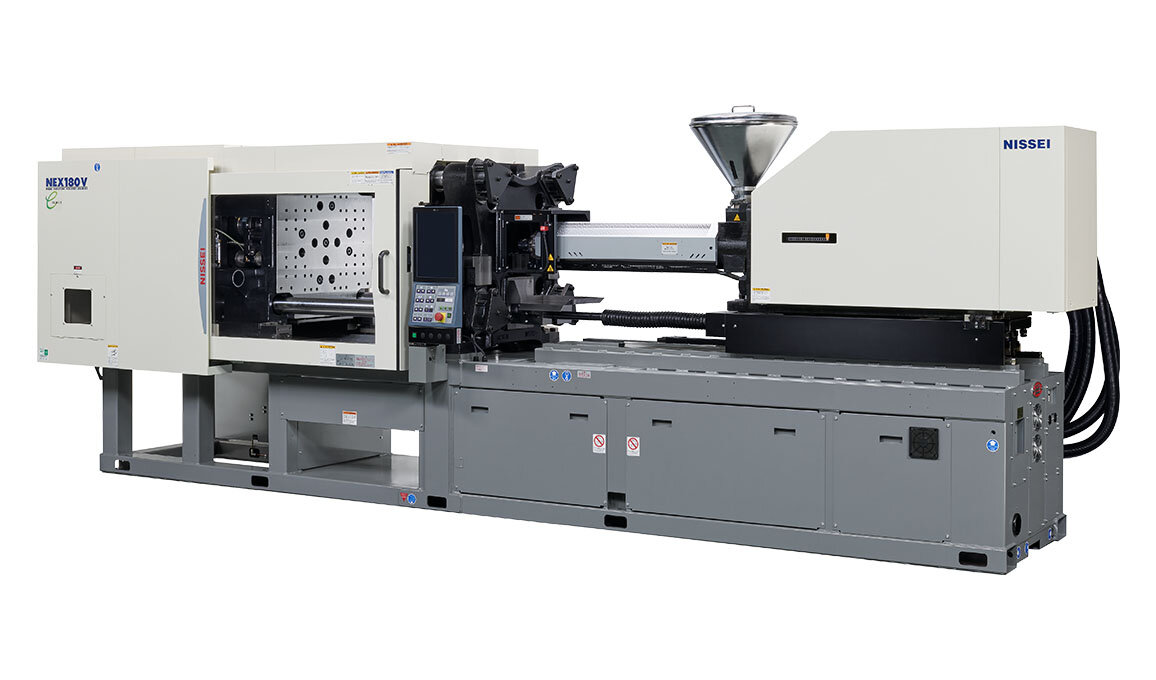
横型成形機は、最も一般的に使用される射出成形機 であり、射出ユニットと型締ユニットが水平方向に配置された構造を持ちます。この形式では、金型が左右に開閉し、成形品が重力によって自然に落下するため、自動搬送や大量生産に適している のが特徴です。
特に、自動車部品、家電製品、日用品などの大量生産を必要とする業界で広く採用 されており、安定した成形が可能なことから、多くの工場で標準的な装置として導入されています。
- 横型射出成型機の構造
横型成形機は、射出ユニットと型締ユニットが水平方向に配置され、金型が左右に開閉する構造 を持っています。この配置により、成形品を重力の影響で自動的に落下させることができ、取り出し作業の効率が向上 します。特に、大量生産や自動化ラインとの組み合わせに適しており、多くの工場で採用されています。
横型成形機の主な構成要素として、射出ユニット(樹脂を加熱・溶融し、射出する装置)、型締ユニット(高い圧力で金型を固定し、成形品を形成する装置)、コントロールユニット(温度や圧力、射出速度を管理する装置) などが挙げられます。これらが連携することで、安定した成形が可能となります。
また、横型成形機にはトグル式と直圧式の2種類の型締機構 があり、それぞれ異なる特性を持っています。トグル式は型締力が強く、大型の製品にも対応しやすい のが特徴です。一方で、直圧式は高精度な圧力制御が可能であり、寸法精度が求められる成形に適している という特性があります。
- 横型射出成型機のメリット
横型成形機の最大の利点は、大量生産に適していること です。金型が左右に開閉するため、成形品は自然に金型から落下し、自動搬送ラインへスムーズに移行 できます。このため、ロボットアームやコンベアと組み合わせることで、成形から製品の搬出までを一貫して自動化することが可能 です。
また、大型の成形品の製造に対応しやすい点も特徴 です。竪型成形機では金型が上下に動くため、成形品のサイズに制限がありますが、横型成形機では比較的大きな成形品でも製造が可能 です。そのため、自動車部品や家電製品の筐体など、大型のプラスチック製品の成形に広く活用 されています。
さらに、操作性が高く、メンテナンスが容易 であることも利点の一つです。横型成形機は、オペレーターが作業しやすい高さに配置されているため、材料の補充や金型の交換がスムーズに行える という特性があります。また、構造がシンプルであるため、定期的なメンテナンスも容易 であり、作業効率が向上します。
安定した生産が可能 という点も大きなメリットです。横型成形機は、長時間の連続運転に耐えられる設計 となっており、均一な成形が可能なため、製品の品質を維持しながら大量生産が行える という強みがあります。
- 横型射出成型機のデメリット
横型成形機には多くのメリットがありますが、一方でいくつかの課題も存在します。まず、設置スペースが大きくなる点がデメリット として挙げられます。横型成形機は水平方向に展開されるため、竪型成形機と比較して床面積を多く必要 とします。そのため、限られたスペースの工場では、レイアウト設計に工夫が必要になります。
また、インサート成形には不向き という課題があります。インサート成形とは、金属部品や他の材料を成形品内に埋め込む加工方法 ですが、横型成形機では金型が左右に開閉するため、インサート材がズレやすく、正確に配置するのが難しい ことがあります。そのため、インサート成形を行う場合は竪型成形機の方が適している とされています。
さらに、取り出し装置が必要な場合がある こともデメリットの一つです。小型の成形品であれば重力によって自然に落下し、取り出しが容易ですが、大型の成形品や特殊な形状の製品では、ロボットアームや自動搬送装置を導入する必要 があり、設備コストが増加する可能性 があります。
その他、メンテナンス時の作業負担が大きくなる 点も課題となります。横型成形機は装置のサイズが大きいため、金型の交換や定期メンテナンスには時間と労力がかかる ことがあり、ダウンタイムが長引くと生産効率の低下につながる可能性があります。
- 竪型射出成型機と横型射出成型機の比較表
竪型射出成型機 | 横型射出成型機 | |
機械の構造 | 射出ユニットと型締ユニットが縦方向に配置 | 射出ユニットと型締ユニットが水平方向に配置 |
成形品の取り出し | 成形品は下方向に取り出される | 成形品は横方向に押し出され、ベルトコンベアなどで搬送 |
設置スペース | コンパクトな設計で省スペース | 比較的大きな設置スペースが必要 |
自動化対応 | インサート成形や手動作業と相性が良い | 自動搬送システムとの組み合わせが容易 |
金型の交換 | 金型の交換が比較的容易 | 金型交換はクレーンや自動システムで対応可能 |
成形の安定性 | 重力の影響を受けにくく、成形精度が高い | 量産向きで安定した生産が可能 |
主な用途 | インサート成形、電子部品、自動車部品、医療機器など | 自動車部品、家電製品、日用品、大量生産品など |
「射出成型機」まとめ
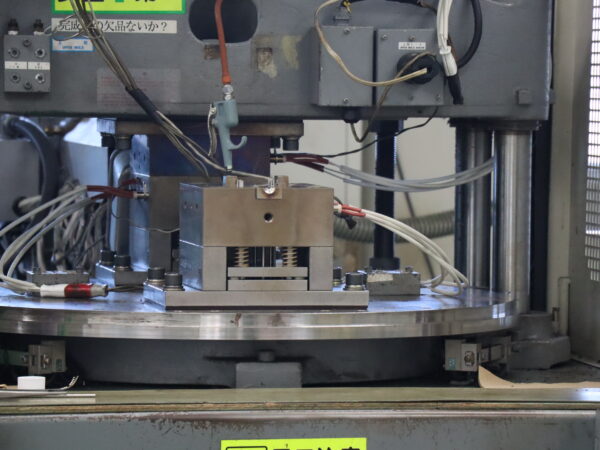
今回の記事では、射出成形機の基本的な概要から、構造やタイプごとの特徴、そして竪型成形機と横型成形機の違いについて詳しく解説しました。
射出成形機は、樹脂を加熱・溶融し、金型へ射出することで成形を行う重要な設備です。電動式と油圧式という駆動方式の違いに加え、竪型成形機と横型成形機といった構造の違いによって、それぞれの用途や特性が異なります。
竪型成形機は、省スペース性やインサート成形のしやすさが特徴で、電子部品や自動車部品などの精密成形に適しています。一方、横型成形機は、大量生産に適した汎用性の高い装置であり、自動搬送システムとの組み合わせによって安定した生産が可能です。
また、近年では、省エネルギーや高精度な成形を実現するため、電動式の射出成形機が増加していますが、高圧が必要な成形では依然として油圧式が多く用いられています。成形品の特性や生産効率を考慮しながら、適切な射出成形機を選定することが求められます。
根本電工株式会社では、射出成形に関する技術と知識を活かし、さまざまな成形ニーズに対応しております。射出成形に関するご相談がございましたら、お気軽にお問い合わせください。

お問い合わせ
Contact
技術的なご相談からお見積りの依頼まで
お気軽にご相談ください。
メールでのお問い合わせはコチラ
お電話でのお問い合わせはコチラ
(0293)24-0567
営業時間:8:00~17:00
お問い合わせ
Contact
技術的なご相談から
お見積りの依頼まで
お気軽にご相談ください。
メールでのお問い合わせはコチラ
お電話でのお問い合わせはコチラ
(0293)24-0567
営業時間:8:00~17:00