医療機器部品とは?特徴と射出成形による製造のポイントを解説

医療の現場では、安全性・耐久性・精度が求められる多種多様な部品が使用されています。近年ではディスポーザブル器具の増加や、検査・診断機器の小型化により、樹脂製の医療機器部品のニーズが急速に高まっています。中でも、射出成形は大量生産に対応しながら高い寸法精度を保てる製造方法として、医療業界で広く活用されています。
本記事では、医療機器の概要や部品に求められる特性、代表的な使用材料、金型設計や成形方法、さらには品質管理や法規制まで幅広く解説します。
医療機器とは?種類と用途の基本知識
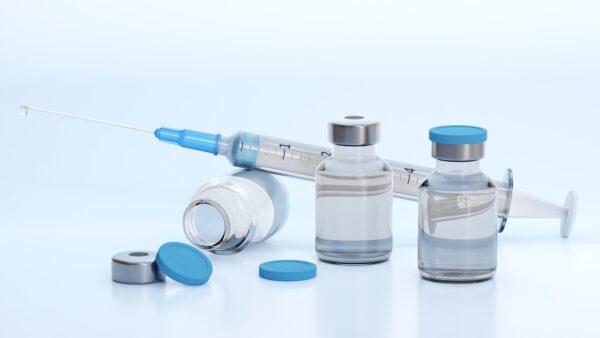
医療機器とは、病気の診断・治療・予防・経過観察などを目的として使用される、機械器具や装置、器材の総称です。注射器やカテーテル等のディスポーザブル器から、CTスキャナや内視鏡のような高機能な検査装置まで、多種多様な機器が存在します。これらの医療用機器は、使用目的や構造、使用部位に応じて分類されており、厚生労働省の薬機法(旧薬事法)によって安全性や品質が厳しく管理されています。
医療機器は大きく「診断機器」「治療機器」「補助機器」等に分けられます。たとえば、診断機器には心電計や超音波診断装置、治療機器には人工呼吸器やレーザーメス、補助機器には手術器具や血圧計などが該当します。また、これらの装置を構成する精密部品や筐体、接続部品の多くは、産業用の高度な射出成形によって製造されています。
さらに、医療機器は使用目的や身体への影響度に応じて、以下のような4つのクラスに分類されています(薬機法に基づく第一区分)。それぞれのクラスは、日本国内での製造・販売において必要な手続きや許可に関連し、厳密に運用されています。
- クラスI(一般医療機器):体温計、メス、注射器など
- クラスII(管理医療機器):X線撮影装置、電子血圧計など
- クラスIII(高度管理医療機器):コンタクトレンズ、輸液ポンプなど
- クラスIV(高度管理医療機器・特定保守管理医療機器):ペースメーカー、人工心肺装置など
クラスが上がるほど、製造や販売における規制や品質管理の基準も厳格になります。特にクラスIII以上の製品は、ISO13485に基づいた厳密な管理体制のもとで製造される必要があり、医療従事者との協力のもと、定期的な調査や製品改善も行われています。
また、使用中の機器についても適切な修理や点検が求められ、保険適用対象となる場合の案内や情報提供も重要です。医療機器の使い方は医療現場での操作性にも直結するため、設計段階からユーザー視点が重視されています。
再生医療や高齢化社会の進展に伴い、今後ますます多様な医療ニーズに応えることが求められます。こうした背景から、医療機器を構成するプラスチック部品には高い精度と信頼性が求められ、射出成形のように量産性と品質を両立できる加工技術のニーズが年々高まっています。
医療機器の部品に求められる特性
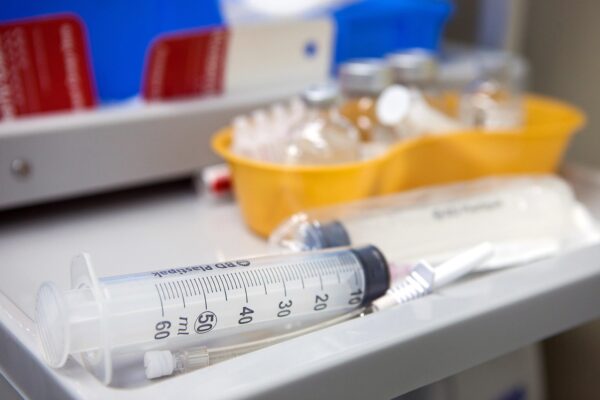
医療機器に使われる部品は、直接人体に接触する機会も多く、非常に高い品質と信頼性が求められます。射出成形によって製造されるプラスチック部品であっても、生体適合性や耐薬品性、滅菌対応性、高精度な寸法管理など、厳しい性能要件を満たさなければなりません。
こうした性能は、製品の用途によっても異なりますが、以下の3点が特に重要とされています。
- 生体適合性
人体と直接接触する部品では、素材に対するアレルギーや毒性、異物反応を引き起こさない生体適合性が必要です。注射器やカテーテル、インプラントなどのパーツには、ISO10993などの生体適合性試験で安全性が確認された材料を使用することが求められます。特にPEEK(ポリエーテルエーテルケトン)などの高機能エンプラは、耐熱性・機械的強度・化学的安定性に優れており、医療用に広く採用されています。
- 滅菌・耐薬品性
医療現場では、繰り返し使用される器具だけでなく、ディスポーザブル製品にも滅菌処理が必須です。高圧蒸気(オートクレーブ)、ガス滅菌、電子線滅菌などさまざまな滅菌方法に耐えられる材料が求められます。また、薬剤や消毒液との接触による変質・劣化を防ぐ耐薬品性も重要です。PP(ポリプロピレン)やTPX、PBTといった素材は、耐薬品性と成形性を両立できるため、医療分野でも多用されています。
- 高精度・高信頼性
医療用プラスチック部品は、ミリ単位ではなく、ミクロン単位の寸法精度が求められるケースも少なくありません。たとえば、注射器のスムーズな摺動性や、接続パーツの密閉性などは、わずかな誤差でも製品機能に大きな影響を与えます。そのため、金型設計や射出成形条件の最適化、成形不良の抑制や異物混入の防止など、製造工程全体にわたる品質管理が強く求められています。
医療機器に使用される主な樹脂材料と成形方法
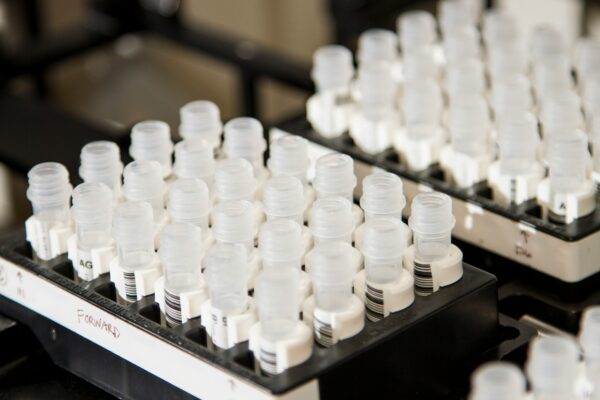
医療機器に使われるプラスチック部品の多くは、射出成形によって製造されています。射出成形とは、樹脂を加熱して溶融し、金型に高圧で射出し冷却・固化させて成形する方法です。大量生産に適しており、高い寸法精度と形状の自由度を両立できるため、医療業界では幅広く採用されています。
医療現場で射出成形によって製造される部品には、注射器やシリンジ、カテーテルのハブ、フィルターケース、診断機器のハウジングなどがあり、ディスポーザブル製品にも多く使われています。
また、金属部品と樹脂を一体成形するインサート成形も医療機器分野で活用されている成形技術です。たとえば、電極やネジ部品を樹脂部に組み込む構造にすることで、強度や導電性といった機能性を持たせながら、部品点数を減らすことが可能になります。製品の機能や使用環境に応じて最適な成形方法が選ばれる点も、医療機器製造の特性の一つとなっています。
- 主に使用される医療用樹脂と特徴
医療機器に使用される樹脂材料は、用途や機能に応じて厳しく選定されます。代表的な使用材料としては、以下のような樹脂素材の一覧が挙げられます。
材料名 | 特徴・用途例 | ||||
PEEK(ポリエーテルエーテルケトン) | 高い耐熱性・耐薬品性・機械強度を持ち、インプラントや長期使用部品に最適。 | ||||
PC(ポリカーボネート) | 高い透明性と耐衝撃性を持ち、保護カバーや観察用部品に使用される。 | ||||
PP(ポリプロピレン) | 軽量で滅菌耐性に優れ、ディスポーザブル医療製品に多用。 | ||||
TPX・PBT・PA(ナイロン)など | 耐薬品性や剛性、成形性に優れ、用途に応じて使い分けられる。 |
これらの材料はそれぞれ成形特性が異なるため、金型設計の段階から射出条件や材料の収縮率、滅菌対応性を考慮した設計が求められます。医療機器における寸法精度・耐久性・安全性を確保するためには、設計・成形・品質管理を一体で考える必要があります。
- 金型設計と寸法精度
医療用プラスチック部品は、非常に小さな寸法誤差が製品の性能や安全性に直結するため、金型設計の精度と成形時の寸法管理が極めて重要です。特に、カテーテルや注射器のような滑らかな動作が求められる部品では、ミクロン単位のズレが使用感や密閉性に大きな影響を与えることがあります。
金型設計においては、樹脂の流動性・収縮率・冷却速度・ガス抜きの処理など、多角的な要素を考慮して最適化を行います。また、PEEKやPCなどのエンジニアリングプラスチックを用いる場合には、高温耐性と離型性の両立も設計時のポイントになります。
さらに、CAD/CAMの3D設計技術や、CAEによる成形シミュレーションを活用し、変形やヒケの発生を事前に予測・回避することが、安定した品質につながります。
- クリーンルーム対応と異物混入対策性
医療機器部品の成形現場では、異物混入は絶対に避けなければならない重大リスクとされます。異物が混入したまま製品として流通すると、患者の体内で炎症や感染を引き起こす可能性があるため、成形時の環境管理が非常に重視されます。
そのため、多くの医療機器メーカーでは、クリーンルーム内での成形・検査・梱包が求められます。特にISOクラス7〜8相当の清浄度を保った生産環境や、静電気・微粒子・油分・水分などの異物対策が実施されます。
また、射出成形機の構造そのものにも、防塵性や清掃性に配慮した設計が必要です。金型の隙間やエジェクターピン周辺など、微粒子が滞留しやすい箇所への対策も重要視されています。
クリーンルーム成形に対応した設備選定と、徹底した生産管理体制は、高信頼な医療部品づくりにおいて重要となっています。
医療機器製造における法規制と品質管理
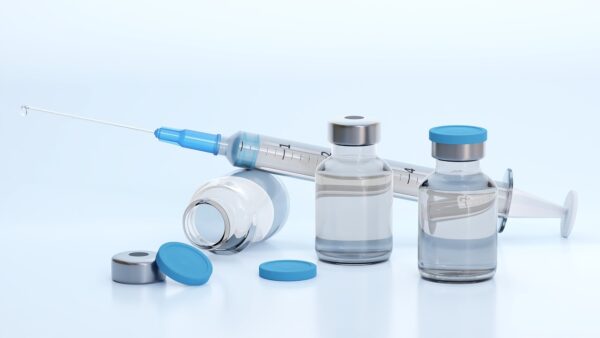
医療機器に使用される部品は、人の健康や生命に関わるものであるため、製造過程では極めて厳格な品質管理と、各種法規制への準拠が求められます。特に射出成形のように大量生産される部品では、一つひとつの製品にばらつきがないこと、そして一貫して高い品質が維持されていることが非常に重要です。
- ISO13485による品質マネジメントシステム
医療機器の製造において、国際的に広く認証取得が進んでいるのが「ISO13485」です。これは医療機器専用の品質マネジメントシステムに関する国際規格で、製品の設計・開発・製造・設置・サービスに至るまで、トレーサビリティや記録の維持、是正措置、リスクマネジメントなどの体制整備を求められます。
特に、射出成形を行う企業では、ロットごとの検査記録、原料ロットの管理、寸法測定の結果などを記録・管理し、万が一の不具合にも迅速に対応できる体制が不可欠です。
- 薬機法への適合と製造販売承認の必要性
日本国内で医療機器を製造・販売するには、「薬機法(医薬品医療機器等法)」への適合が必須です。製造業者には「医療機器製造業許可」、製品の販売には「製造販売業許可」や「製造販売承認」が必要であり、それぞれのクラス分類(I〜IV)に応じた審査や届け出が義務付けられています。
特に、クラスIII・IVに該当する高度管理医療機器の部品製造を行う場合には、品質管理体制の強化や、第三者機関による認証取得が必要となります。
加えて、以下のような体制整備も求められます。
- 医療機器製造業登録
医療機器の部品を含む製造を行うには、製造所単位での登録が必要です。 - 医療機器製造販売業許可
医療機器として市場に供給する企業には、製造販売業の許可が求められます。外注生産を行う場合でも、販売元が取得している必要があります。 - 製造管理者・品質管理者の配置
品質管理体制の整備の一環として、製造所には資格を有する管理者の常駐が義務付けられています。 - GMP(適正製造基準)への適合
特にクラスIII・IVに分類される医療機器を製造する場合には、設備・文書・工程管理などにおいてGMPに準拠した運用が求められます。
これらの体制を構築することで、製品の安全性・信頼性の担保と、万が一の不具合発生時におけるトレーサビリティの確保が可能になります。
- 検査体制と異物管理
医療用射出成形品では、外観・寸法・機能などの検査工程も非常に重要です。製造ライン上では、CCDカメラによる外観検査や三次元測定機による寸法検査、リークテストによる密閉性検査など、各種の自動・手動検査が行われます。
また、異物混入を防ぐために、製造現場のゾーニング管理・静電気対策・人の動線管理など、細やかな対策が求められます。これらの管理レベルが、製品の信頼性と安全性を大きく左右します。
医療機器分野における射出成形の今後と可能性
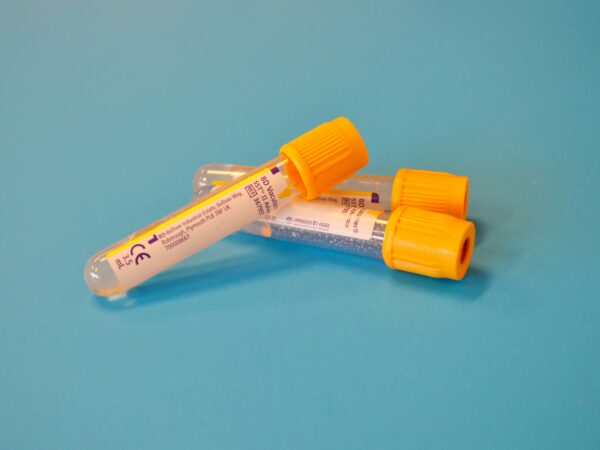
医療現場では今後も、安全性・操作性・衛生性を重視した製品開発が求められており、部品製造における射出成形の役割はますます大きくなっていくと考えられます。特に近年は、以下のような技術革新や医療ニーズの変化が進行しています。
- 高機能樹脂材料の進化
材料開発の分野では、PEEKやPPSU、TPXなど、医療用に適した高機能樹脂のバリエーションが増えています。これらの材料は、滅菌への耐性・透明性・薬品への耐久性・繰り返し使用による劣化の少なさなどを備えており、従来では金属やガラスが使われていた用途でも代替が進んでいます。
今後も材料メーカーと成形加工メーカーの連携が進み、新たな医療アプリケーションに対応できる製品の創出が期待されます。
- 微細・高精度成形技術の進化
微細化・複雑化が進む医療機器部品のニーズに対し、射出成形でも金型精度の向上やマイクロ成形技術の進化が進んでいます。特にマイクロ流路を持つ診断デバイスや、微小部品を組み込む医療用センサーなどでは、ミクロン単位の精度で成形が求められ、金型加工・成形条件制御・検査工程の高度化が不可欠となります。
また、3Dプリンタと金型製作を組み合わせることで、試作や少量多品種対応のスピードアップが可能になり、今後の医療機器開発サイクルを加速させる要因となるでしょう。
- 環境対応とサステナビリティへの対応
医療機器分野でも、環境負荷の少ない材料選定や生分解性プラスチックの活用など、持続可能性を意識した設計・製造への転換が始まっています。ディスポーザブル製品が多い中で、素材リサイクルや製造エネルギーの最適化といった視点が求められています。
成形技術と材料技術の両面からサステナブルな製品開発を進めることが、医療業界における新たなスタンダードになりつつあります。
まとめ
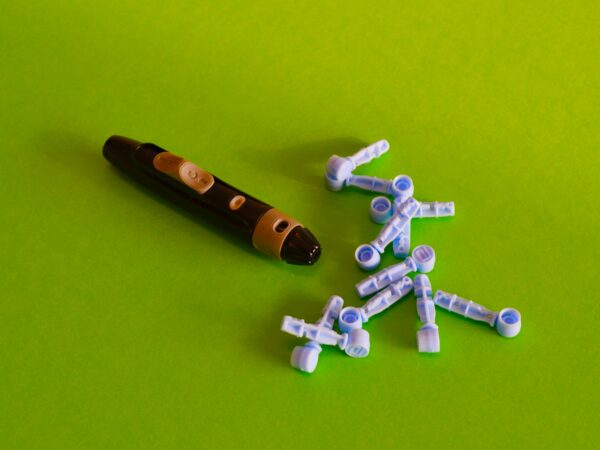
医療機器は、人命や健康に直結する極めて重要な分野であり、その製造には高い安全性、信頼性、そして厳格な品質管理体制が求められます。中でも射出成形は、ディスポーザブル製品や機能部品の製造において欠かせない加工技術であり、精度・生産効率・量産対応力を兼ね備えた手法として広く活用されています。
近年では、医療現場に求められる製品の多様化に伴い、使用樹脂の高度化、金型設計の精緻化、クリーンルームでの異物混入対策といった成形技術の高度化が進んでいます。さらに、インサート成形や複合成形などの応用技術の導入により、複雑構造や高機能部品への対応も可能となりつつあります。
また、ISO13485やGMP(適正製造基準)への対応をはじめ、医療機器に関わる法規制や認証制度に準拠した生産体制の構築も欠かせません。今後は、デジタル技術の導入や環境配慮型材料への対応など、新たな課題にも積極的に取り組むことが求められます。
射出成形は今後も、医療機器の高度化と医療ニーズの進化に伴い、その存在価値をさらに高めていくと考えられます。
根本電工株式会社では、長年にわたり射出成形による医療用プラスチック製品の製造に取り組んでまいりました。高精度・高品質な製品づくりの実績とノウハウを活かし、お客様の多様なニーズにお応えいたします。医療機器向けプラスチック部品の製造に関するご相談がございましたら、どうぞお気軽にお問い合わせください。

お問い合わせ
Contact
技術的なご相談からお見積りの依頼まで
お気軽にご相談ください。
メールでのお問い合わせはコチラ
お電話でのお問い合わせはコチラ
(0293)24-0567
営業時間:8:00~17:00
お問い合わせ
Contact
技術的なご相談から
お見積りの依頼まで
お気軽にご相談ください。
メールでのお問い合わせはコチラ
お電話でのお問い合わせはコチラ
(0293)24-0567
営業時間:8:00~17:00